Five Questions to Ask When Selecting a Bulk Solids Sampler
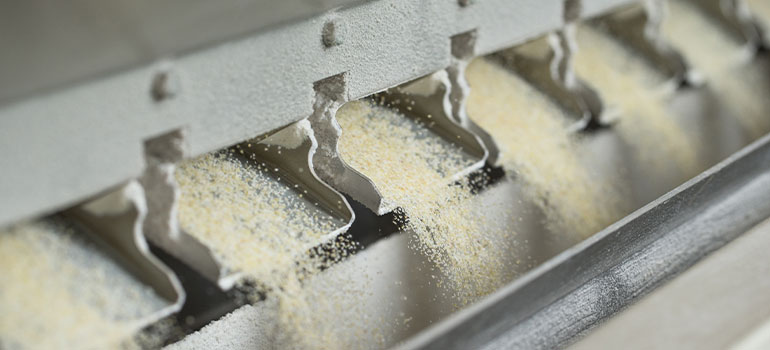
Let’s say you have a large order for a dry powdered food product. You need to be sure the product fits the customer’s specifications before it’s shipped, or you need to keep tabs on the moisture content of your material throughout a processing run, or you need to ensure that your chemical material doesn’t rise above a certain level of volatility. To accomplish these tasks, you’ll need to accurately sample and test the material using a sampler that can enter the material stream, capture a statistically significant quantity of that material that is representative of the process. For the most accurate and repeatable sampling, you will need to employ a method that limits bias and allows precise samples to be taken at regular intervals, leaving no room for error – an automatic sampler.
1. HOW DOES AN AUTOMATIC SAMPLER FOR SOLIDS AND POWDER WORK?
Automatic samplers are available in three basic sampling modes and three common operating types. Sampling mode refers to how the sampler collects the sample: The spot sampler enters the material stream and takes a sample only at the point where it stops; the strip sampler enters the material stream and takes a sample from a portion of the stream all the way across the stream and the cross-cut sampler takes a sample from the stream’s entire cross-section. The cross-cut sampler will give the most representative sample of your material. Application, process location, and access are some factors that determine the best Sampling Mode.
The operating type describes the automatic sampler’s material-collecting mechanics. The tube or tube probe sampler is the simplest and most common. Basically, it’s a tube with a hole near one end. The hole end of the tube moves into the material stream, material flows into the hole, and the tube retracts from the material stream. The tube-and-auger sampler type also is a tube with a hole in it, but an auger in the tube helps move the flowing material into the sampler. The third type of sampler is the pelican diverter or pelican sampler, called this because of the vague similarity between the sample cutter (the component of the sampler that passes through the material stream and cuts out a sample) and a pelican’s beak: Both have an opening at the top with a “container” hanging down from the opening.
In all three operating types, a motor or pneumatic device activates the sampler, causing it to enter and withdraw from the material stream. The material flows into the sampler and then is released either by mechanics or gravity into a sample container that’s manually or automatically removed to your analysis device or quality control personnel. Again, all three types of automatic samplers can be used depending on the application, process location, and access.
2. WHY AM I TAKING THE SAMPLE?
Reasons to sample include the need to analyze material particle size, composition, physical characteristics, and contaminants for process and quality control and to meet regulatory compliance; control material physical appearance, and retain a sample for your or your customer’s future reference for raw material inspection or shipping authorization. Your sampling will need to be accurate and provide repeatable results.
3. WHAT ARE MY MATERIAL’S PHYSICAL PROPERTIES?
Your material’s physical properties will dictate the sampler’s particular sampling mode and operating type. You need to know:
- Material flowability
- Particle size and density
- Material moisture content
- Material temperature
- Ambient temperature
- Target contaminants
- Distinctive material qualities (Is your material abrasive, corrosive, sticky, friable, or hazardous? Is it homogeneous? Does it tend to segregate?)
Knowing these qualities will help you choose the sampler’s materials of construction and any optional equipment needed for the unit to function properly in your application.
4. WHERE WILL I LOCATE THE SAMPLER?
Process location (like final bagging) and space restrictions at your desired sampling location will be major factors in your sampler choice. For example, a tube sampler is typically mounted at a 45-degree angle off your equipment, while a tube-and-auger sampler can be mounted horizontally. If either sampler will work for your application, and space is at a premium, you may want to go with the tube-and-auger sampler.
5. HOW DO I CHOOSE A MODEL?
A range of samplers is available in all of the basic sampling modes and operating types, in varying configurations. Once you know what mode and type you need, your representative can help you select a specific model. In addition to the factors already discussed, the following factors also will help determine which model best suits your application:
· Available utilities for powering the sampler
· Equipment the sampler will be interfaced with
· Specific point in the process (packaging, mixing, etc)
· The sampler’s control method
It’s important to consider all factors before selecting your automatic sampler. Discuss your specific needs, both in terms of your application requirements and practical considerations like size and cost, with your sales representative. Together,
you and your representative can determine which sampler model best fits your requirements and create and customize the proper sampler for your application.
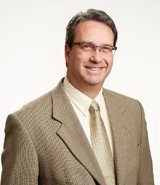
Written by John Powalisz
John Powalisz, Director of International Sales, is dedicated to sharing his technical expertise and knowledge of sampling equipment and systems in power plants, refineries, chemical and food processing facilities garnered from more than 19 years with the company. John has worked with clients worldwide to help them to comply with regulations and optimize processes by applying proper sampling hardware and techniques. While he is well-versed in all Sentry products and applications, he is particularly focused on the food and beverage and power generation markets as well as emerging market development.
Related Posts

Bulk Solid
CASE STUDY: Replace Your SWAS Panels
In terms of total annual net electricity generation, this power plant is ranked #44 out of 11,979 power plants nationwide.
Read More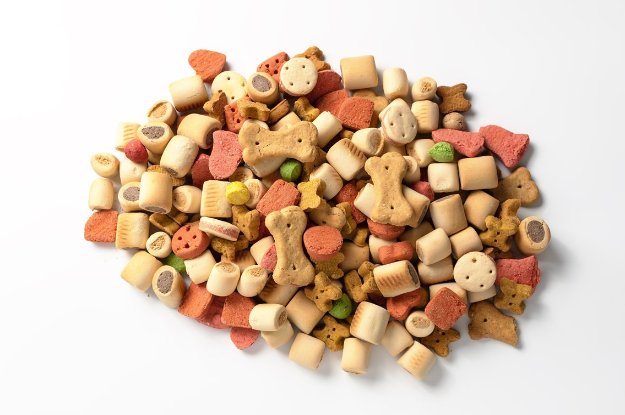
Bulk Solid
Maximize Recipe Control with Automatic Sampling
A repeatable, representative sampling of bulk-solid products is essential in today’s production environments. From food production to plastics, automatic samplers are becoming standard practice to provide the needed insights on product quality and safety for profitable production.
Read More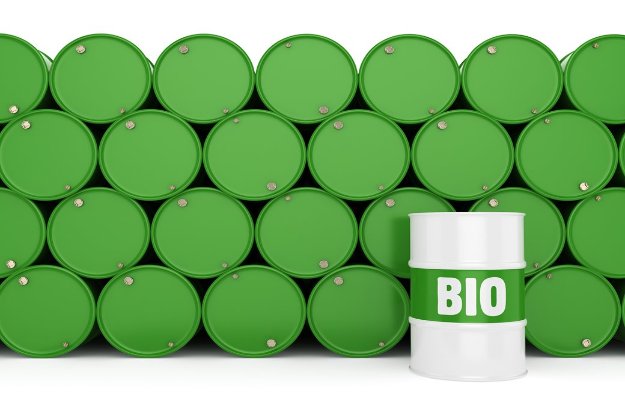
Bulk Solid
Why is Hydrocarbon Sampling Important?
Renewable hydrocarbon biofuels are fuels produced from biomass sources, including vegetable oils, animal fats, and specialized crops. They are chemically identical to standard petroleum-based products and can be used in existing engines and infrastructure. However, like petroleum-based products, biofuels require strict testing.
Read More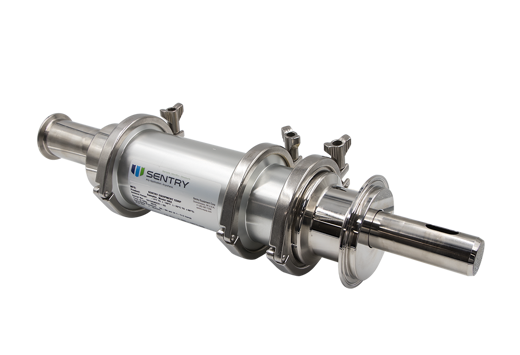
Designed with You in Mind
Shop our complete line of Bulk Solid Samplers to find the right fit for your sampling application.