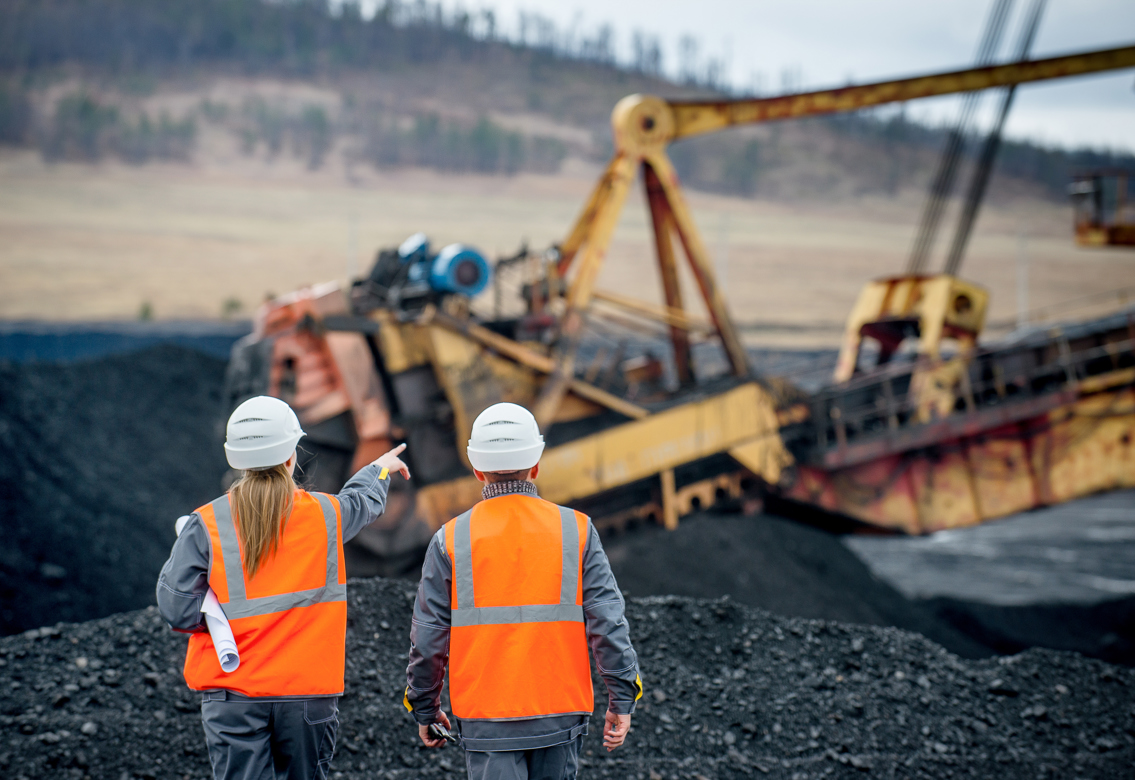
Lithium is a highly reactive and flammable alkali mineral that’s also used in ceramics, smartphone touchscreens, lubricating greases, polymer production, and air treatment. It is a silvery-white metal that is the lightest weight metal known to man and is often used in plant expansion projects as well as new large production projects.
According to the latest figures from the US Geological Survey (USGS), global lithium production in 2019 reached around 77,000 tonnes. Most lithium mining and exploration are located in South America’s “lithium triangle” near Chile, Argentina, and Bolivia. Other top-producing countries include Australia, China, and Zimbabwe. Some of these countries have declared Lithium as a strategic metal.
Lithium is a key strategic metal in the United States as well. The US Senate included lithium more than a decade ago in its Critical Minerals Policy Act of 2011.
Sampling lithium is more important than ever to ensure the product you're delivering is a high-grade lithium concentrate, free of impurities and ready for highly sensitive applications.
The challenges of lithium Mining
Because lithium is highly reactive, it’s not found on its own in nature – it’s present as a constituent of salts or other compounds. Most extracted lithium comes in the form of lithium carbonate, a more stable material that can be transformed into useful compounds, pharmaceuticals, and other industrial products.
Lithium salts can be found in underground deposits of clay, mineral ore, and brine, as well as in geothermal water and seawater. Two of the most prominent methods of mining lithium are the mining of spodumene ore and extracting lithium from salt flats.
To ensure accuracy when extracting lithium or mining spodumene, determining lithium concentration is fundamental. Sampling techniques and the efficiency of extraction processes ensure the market is driven forward and becomes more environmentally sound.
Mining Spodumene Ore
Spodumene is a pyroxene mineral that’s found in lithium-rich pegmatites, an igneous rock that forms during the final stage of magma's crystallization. It’s also usually associated with other lithium minerals such as lepidolite, eucryptite, and petalite.
The largest concentrations of lithium-containing minerals are found in granitic pegmatites, including spodumene. Due to its high lithium content, spodumene is considered the most important lithium ore mineral.
Physically separating lithium minerals can be performed by wet and dry screening, tabling and magnetic, electromagnetic, electrostatic, magnetohydrostatic bullet, and heavy media separation. You can then further process the flotation concentrate with high-temperature or chemical processes to produce valuable lithium compounds.
Lithium can also be extracted from spodumene concentrates after roasting operations. Spodumene will go through a phase transformation during roasting, which is performed at about 1050°C. After this, it’s cooled and mixed with sulphuric acid, then roasted again at about 200°C. At 170°C, an exothermic reaction starts, and lithium is extracted to form water-soluble lithium sulfate.
SAMPLING FOR LITHIUM MINING
No matter what method is used to extract lithium from the earth, specialized samplers can help ensure coarsely crushed samples or liquid brine samples are delivering a high-grade, impurity-free lithium concentrate.
Sampling also determines the amount of usable material in a particular “run” of lithium concentrate. Similar to taking a representative sample in gold mining, it guarantees you’re getting the highest material return for your labor. Sampling is useful whether you’re sampling ore, or utilizing lithium salts gathered from mineral beds in the desert.
Representative sampling can also occur after lithium has been obtained to optimize the separation and refining process of the finished material. A common representative sampling application across many lithium producers is a sampling of the finished product as it is loaded and measured on an approved weigh scale.
Lithium mines in Western Australia and Chile have found success with sampling in both ore mining and salt-bed extraction. An automatic point sampler, such as the Sentry ISOLOK SAK, provides representative samples of liquids and slurries such as waste acid, resin bead slurry, bauxite mud and raw municipal sludge – and deposits that contain lithium.
By capturing a fixed volume of material with a sealed design, automatic point samplers keep the operator isolated from the process and the container locked out from external influences. The separation of operator and external influences ensures that these highly volatile compounds are meeting necessary benchmarks in the most efficient way possible.
The unique challenges posed by the lithium mining process require an in-depth understanding of bespoke automatic sampling technologies.
Sentry Equipment offers the proven capability to streamline these processes, in order to help provide the highest level of quality and efficiency to our end-users in the mining industry.
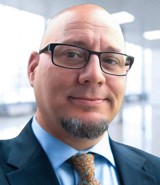
Written by Nate Leonard
Related Posts

Bulk Solid
CASE STUDY: Replace Your SWAS Panels
In terms of total annual net electricity generation, this power plant is ranked #44 out of 11,979 power plants nationwide.
Read More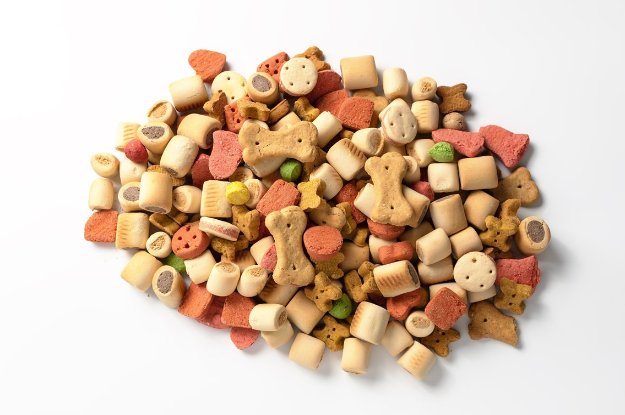
Bulk Solid
Maximize Recipe Control with Automatic Sampling
A repeatable, representative sampling of bulk-solid products is essential in today’s production environments. From food production to plastics, automatic samplers are becoming standard practice to provide the needed insights on product quality and safety for profitable production.
Read More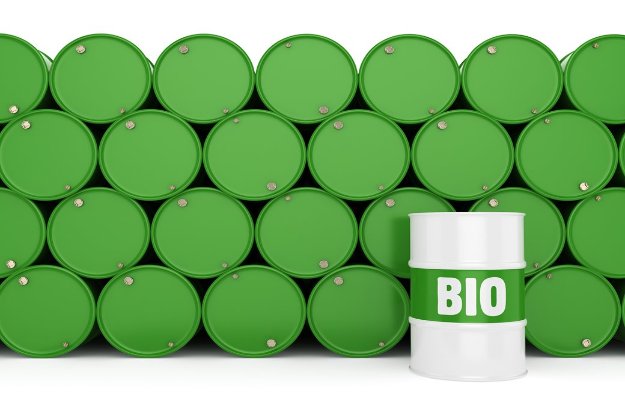
Bulk Solid
Why is Hydrocarbon Sampling Important?
Renewable hydrocarbon biofuels are fuels produced from biomass sources, including vegetable oils, animal fats, and specialized crops. They are chemically identical to standard petroleum-based products and can be used in existing engines and infrastructure. However, like petroleum-based products, biofuels require strict testing.
Read More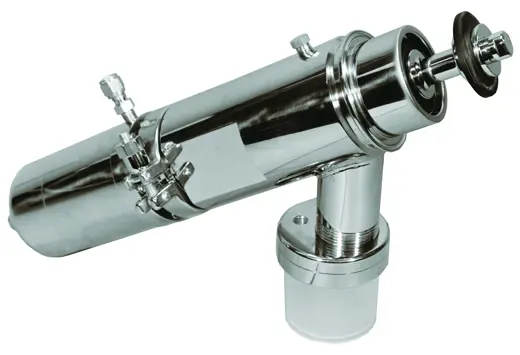
Designed with You in Mind
Shop our complete line of ISOLOKs to find the right fit for your sampling application.