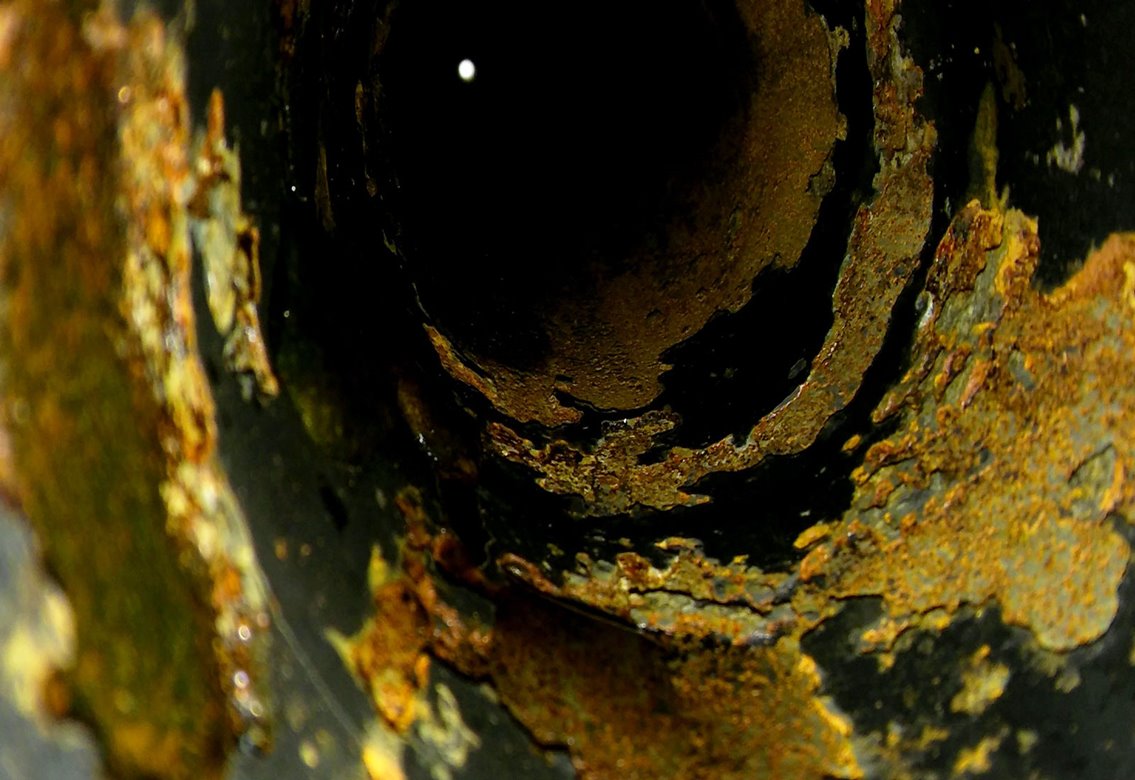
Pipelines carrying oil and gas experience internal corrosion when water is present inside the lines.
The amount of corrosion will vary, depending on factors such as temperature, total pressure, CO2 and H2S content of the gas, pH of the water, flow conditions, use of inhibiting chemicals and more.
But no matter the amount of corrosion, it can have devastating effects on your equipment.
That’s why the Pipeline & Hazardous Materials Safety Administration, part of the U.S. Department of Transportation, mandates:
“Each operator must develop and implement a monitoring and mitigation program to identify potentially corrosive constituents in the fluid being transported and mitigate the corrosive effects.”
Pipeline Pigging isn't enough
To maintain pipeline integrity, many facilities use cleaning pigs within the pipelines to flush out water and prevent corrosion.
Oil and Gas Companies often decide not to conduct additional monitoring for internal corrosion based on the false belief that running pigs through the lines clears out the water from every portion of the pipe.
Monitoring within non-piggable lines is crucial, but even piggable systems aren’t exempt from the need for internal monitoring. Regardless of the type of line, choosing where to monitor is critical to your program’s success.
4 Steps to internal corrosion monitoring
1. Do a Quick Check with a Drip Pot
If you’re not sure if you have internal corrosion, you can perform a quick check by creating a low spot on your system with a drip pot assembly. This assembly provides a sample of all liquids in the system, as well as a corrosion coupon monitor and a bacteria collection device. This is also a great method for proving your chemical corrosion inhibitor program.
2. Choose Your Internal Monitoring Method(s)
- Flush-mounted weight loss coupons
- Flush-mounted electrical resistance (ER) probes
- Under-the-pipe drip pot assemblies
3. Identify Locations to Monitor for Corrosion
One way to identify monitoring locations is through process flow profiling.
Flow profiling is used to predict where water might travel and settle out of the process fluids. Water generally accumulates lower in the system and is swept upward with the process fluids. The sweeping is velocity dependent. Therefore, profiling where the velocity will change, such as pipe diameter changes and direction of flow changes, can determine where you should monitor.
Locations prone to corrosion and require monitoring include:
- Drips
- Separators
- Storage
- Low Spots in the Pipe
- Headers
- Dead Legs
- In Front of Damming System Components (Valves, Regulators, Orifice Plates, etc.)
4. Determine Monitoring Position
Monitoring occurs horizontally or vertically and requires varied methods of measurement and devices to execute.
Monitoring on a horizontal line requires the measurement element to be positioned close to but never touching the bottom of the line. Water is heavier than hydrocarbons, so it will settle along the bottom of the pipe. Because of this settling, you will want to position ER probes, UT probes and coupons near the bottom on a horizontal line and mount them from the 12:00 or 6:00 o’clock position regardless of the process type.
Monitoring on a vertical line, however, will require positioning the measuring element at the center of the flow. This is due to the positive process fluid movement being at the center of the pipe, away from the friction of the pipe walls.
By following these steps, you will help prevent corrosion before it even starts, keeping your equipment up and running longer.

Written by Lance Witt
With over 25 years in the hydrocarbon industry, Lance Witt brings an unique perspective to Sentry Equipment as the Regional Sales Manager. He is a wealth of industry knowledge as an author and presenter fpr ASGMT, ISHM, AFMSC and Gas Well Deliquification Workshops. He is also a technological expert with 3 patents on chemical optimization and an active NACE member.
Related Posts
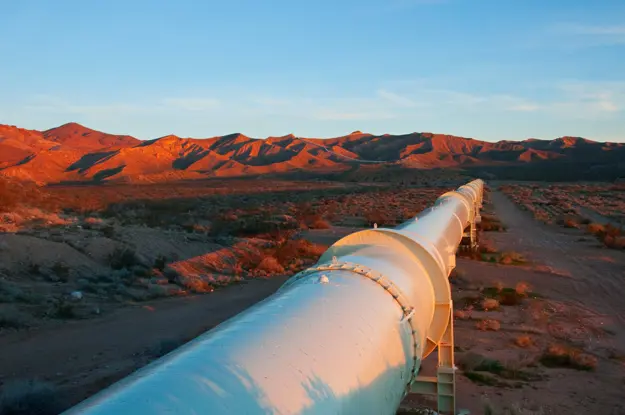
Corrosion
PHMSA Mega Rule: Your Guide to Navigating the New Regulations
The pipeline Industry has heard a lot about the Pipleine and Hazardouse Materials Safety Administrations (PHMSA) three rules to reduce the frequency of pipeline failures. Now, the third and final rule has been released.
Read More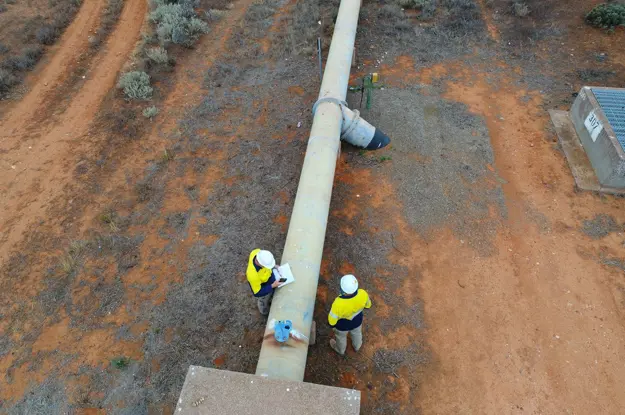
Corrosion
What are Atomizers and Do I Need Them?
Corrosion is a significant contributor to gas and oil pipeline failures. That is why many oil and gas companies implement chemical treatment methods to eliminate corrosive contaminants within gas pipelines. But chemical efficiency can be drastically affected by improper injection methods.
Read More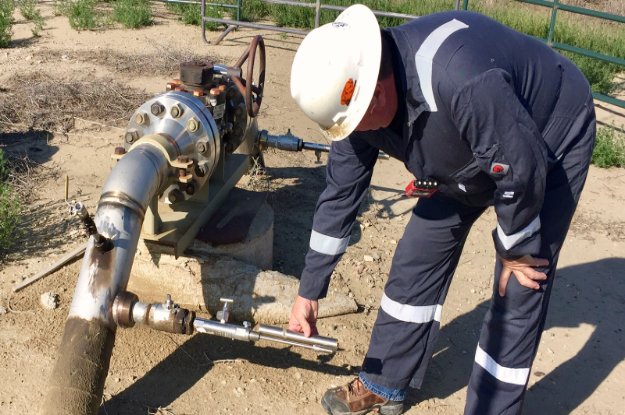
Corrosion
How to Choose Your Internal Corrosion Mitigation Method
Internal corrosion monitoring is critical to preventing and addressing corrosion inside gas and oil pipelines. It is also the first step in choosing the right corrosion mitigation method based on identified corrosive constituents.
Read More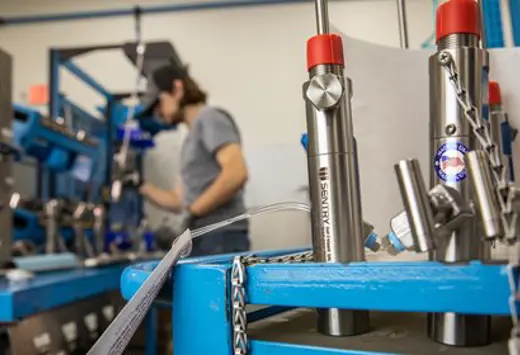
Mitigate Pipeline Corrosion
Sentry's complete line of corrosion protection products will maximize your pipeline's longevity.