How to Increase the Efficiency and Output of Your Evaporator
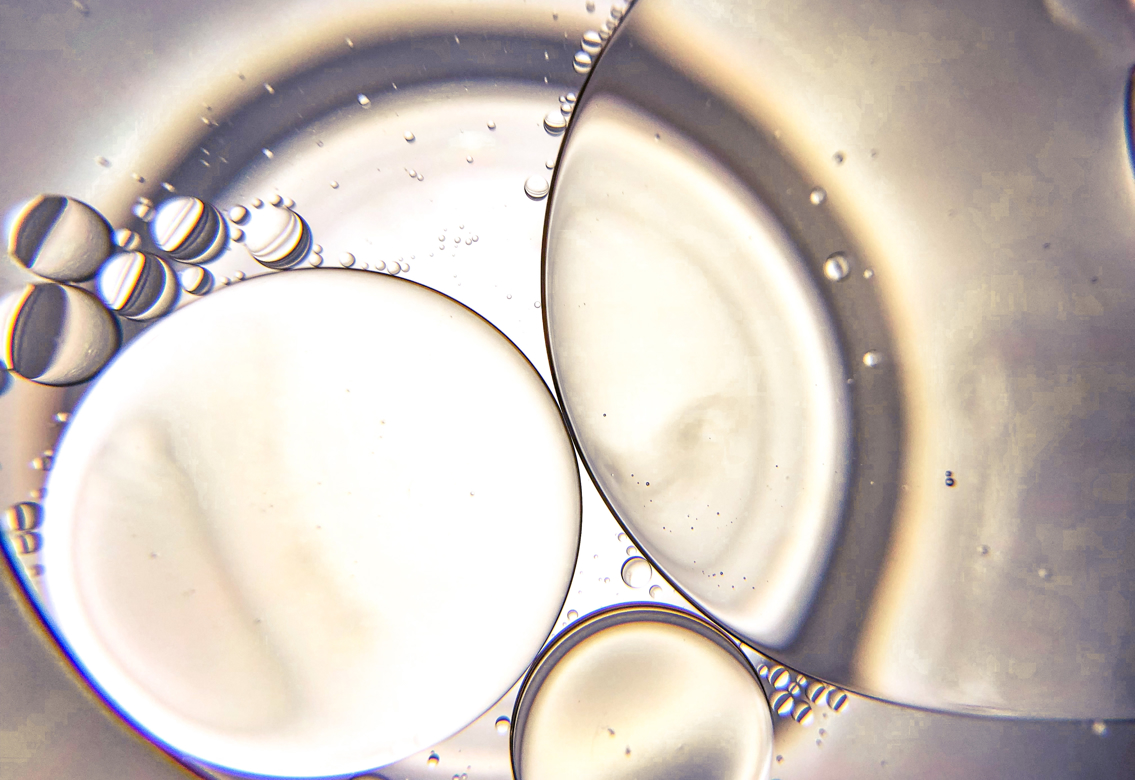
As EPA (Environmental Protection Agency) expands regulations and enforcement on the discharge and disposal of industrial fluids from metalworking and metal-finished plants, we can see more equipment being purchased to treat and or solve tSmartSkim Recycling & Filtrationhe problem of waste.
With the ever-changing increase of technology as well as the growth of vendors in the treatment/reduction market, there has been a corresponding increase in dissatisfaction from the end-user. In many cases, the equipment is being asked to perform in a way that it is not designed for or intended. This problem comes from the customer, manufacturer, or representative not fully aware of the type of volume of contaminants in the solutions that need to be eliminated and their effect on the rate and efficiency of the specific treatment process.
However, one product, the evaporator, has gained strength in the market because of its easy-to-understand concept for contaminant elimination. Due to most of the fluid being water (as high as 99% in some cases), we can evaporate the water phase to the atmosphere or a condenser and be left with the concentrate. The rate of evaporation of evaporation is a function of time and temperature, we are changing water to vapor which can be then vented to the atmosphere. The five main reasons for the popularity of evaporators are:
- No discharge to sewer
- Volume reduction
- Moderate capital expenditure
- Compact design
- Easy to understand
Common Problems evaporator users encounter
Many systems are not running the way they are designed or according to the specs given. The main problems encountered are:
- Evaporation rates are generally not as advertised or expected.
- Questionable quality of air discharge
- An oily residue was found on the outside roof or structure.
- Higher temperatures needed for evaporation, increasing safety concerns and cost of operation.
- Needing maintenance for oil and sludge removal
- Odors
Steps for incorporating an evaporator into your waste disposal system
-
Analyze the type and volume of the contaminants that you will see in the waste solution to be processed.
-
Evaluate pretreatment options against your goals and financial limitations.
The more contaminants you remove prior to your evaporator, the more it will impact the process rate, improve air quality, and lower maintenance associated with the upkeep of the evaporator.
Pretreatment Options
To maximize the productivity of your evaporator, the gross amount of oil and solids should be removed before the solution is fed into the evaporator.
The three pretreatment options available are:
Tramp Oil Separators for the removal of free oil (crude oil that has not been absorbed and is accessible for removal) and mechanically dispersed oil depending on the device.
- Oil Skimmers such as wheels, belts, ropes, and mop-type skimmers.
- Coalescers with plastic media, tortuous path
- Open Channel Coalescers like the Crossflow and vertical separators
- Chemically splitting
- High-speed centrifuge
- Simple settling
Solids Filtration for the removal of particulate matter down to as low as 0.5 to 1 micron, but generally more in the range of 10-25 microns.
- Bag or Cartridge Filter
- Magnetic Filter
- Paper Bed Filters
- Solids Centrifuges
- Dredge/Drag out Tanks
- Settling Tanks
Membrane Filtration for the removal of emulsified oils and suspended solids down in the submicron range, from 0.1 to .005 microns.
- MicroFiltration
- UltraFiltration
By pretreating your waste stream and feeding your evaporator with a solution relatively free of oil and gross solids, you can expect to achieve higher processing rates and few shutdowns due to required cleanouts and maintenance. The Sentry Equipment team is here to help you find the solutions you need. Contact us at +1-262-567-7256, or complete our online contact form for more information.
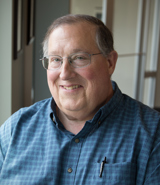
Written by Bill Gimbel
Related Posts
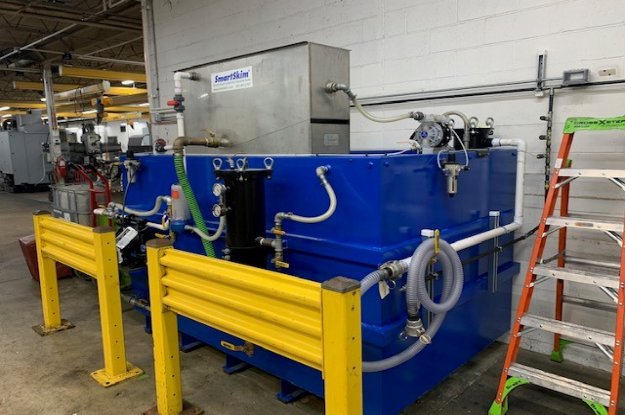
Oil Separation/Coolant Recycling
CASE STUDY: How to Increase the Efficiency of your Facility with Used Equipment
Read More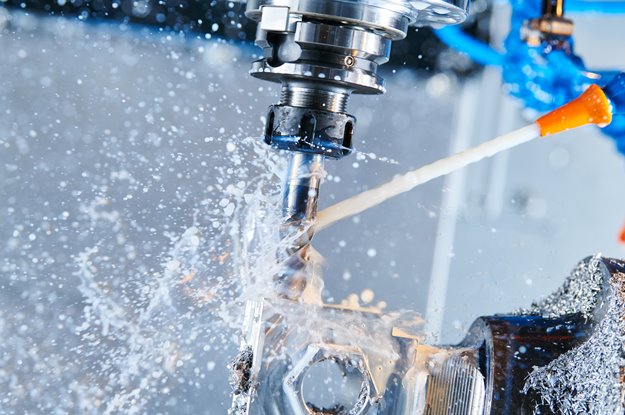
Oil Separation/Coolant Recycling
Reduce Operation Costs with a Coolant Recycling System
Manufacturing processes are inundated with lubricants and other industrial fluids. Managing these fluids is critical to protecting equipment and ensuring worker safety.
Read More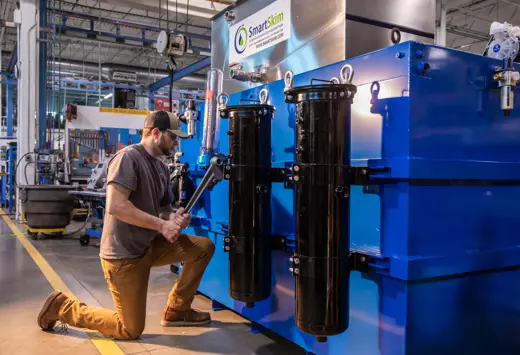
Maximize Manufacturing Processes
Sentry's SmartSkim product line can help maximize your manufacturing processes with coolant recycling and oil separation technology.