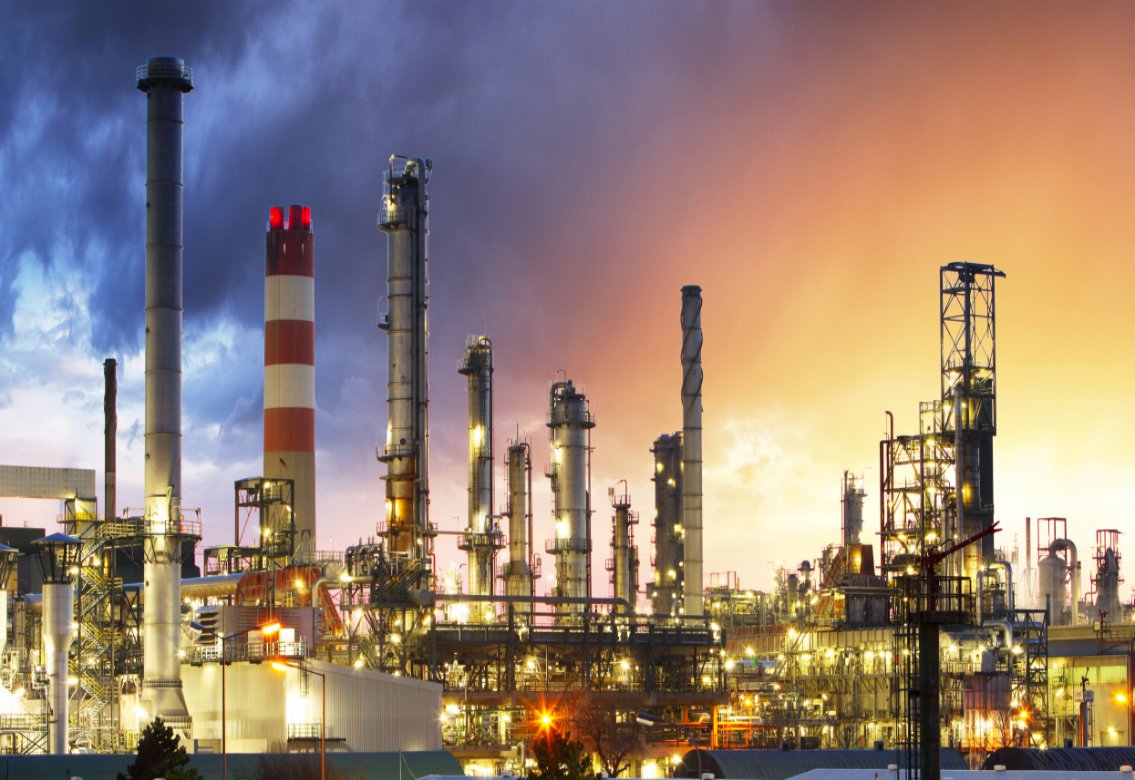
Oversimplifying or ignoring steam and water sampling in combined steam and power plants can lead to significant problems, including operator error, equipment damage, injuries to personnel, and incomplete or inefficient power production.
By following these five key sampling locations in your industrial steam system, you can ensure reliable steam production.
Establishing a properly configured Steam and Water Analysis System (SWAS) can help co-generation plants improve their steam and water process. But simply establishing a SWAS isn’t enough to mitigate the damage. Choosing the right locations for sampling points is critical to maximizing the reliability of your boiler system.
5 KEY SAMPLING POINTS IN A STEAM AND WATER SYSTEM
These are the five locations ASME recommends sampling in your industrial steam system.
1. Make-Up Water – Source water needs to be chemically and physically treated by zeolite softeners, reverse osmosis, or demineralization to achieve a high purity state. Sampling ensures the water is high in purity and won’t introduce contamination to the rest of the system.
2. Boiler Feedwater – This water is comprised of make-up water and condensate. Before it’s fed into the boiler, it must be treated with chemicals (volatiles), such as ammonia.
Careful sampling and control of feedwater chemistry can eliminate and reduce operating costs by minimizing scaling and corrosion, extending the time between chemical cleanings of the boiler. It can also allow higher cycles of concentration in the boiler.
3. Boiler Drum Water – Water in the boiler consists of boiler feedwater and added boiler chemistry treatments, such as phosphates or caustics. Impurities and concentrates must be blown down to prevent equipment damage or failure.
Sampling provides the insight necessary to properly manage the blowdown process and remove excess impurities before they cause issues in the boiler, which can lead to improved chemistry control.
4. Steam – When the water in the boiler drum boils, it produces the steam used to generate power or support the function of critical industrial processes. However, some components of the water carry over into the steam, including some chemical treatments and contaminants.
Steam contamination can be caused by improper boiler water chemistry and failure of boiler mechanical internals (steam separators). It can also be triggered by operational issues, such as the drum level being too high and pushing liquid into the steam pipe, or the drum level being too low and causing poor water chemistry.
Sampling ensures the steam is free of impurities that could negatively affect the power or industrial process production.
5. Condensate – This is condensed steam that has passed through process components. Although it’s usually clean, condensate can get contaminated quickly by process leaks. Sampling ensures that any contamination is detected before it goes back into the cycle.
BENEFITS OF SAMPLING AT ALL 5 LOCATIONS
While some industrial plants sample at only a few of these locations, there are clear benefits to sampling at all five of them.
- Minimize corrosion
- Reduce costs associated with corrosion
- Maintain optimum boiler chemistry
- Reduce plant downtime
- Reduce deposition on turbine blades or in-process components caused by carryover of impurities in the steam
- Extend the life of plant components, including condenser, turbine, and boiler tubes
- Reduce the need for expensive chemical cleaning or tube replacements
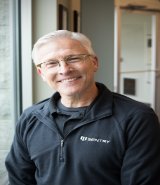
Written by Jeff McKinney
As an industry manager for chemical and petrochemical refining, Jeff is an expert in those markets and is experienced in power generation as well. Jeff is focused on serving these key markets and sharing information on how Sentry sampling and monitoring products and systems can meet any petrochemical or chemical application, anywhere. He is responsible for our market strategy and product offerings, and is alwasy interested in exchanging information on specific industry applications and solutions that meet customer needs.
Related Posts
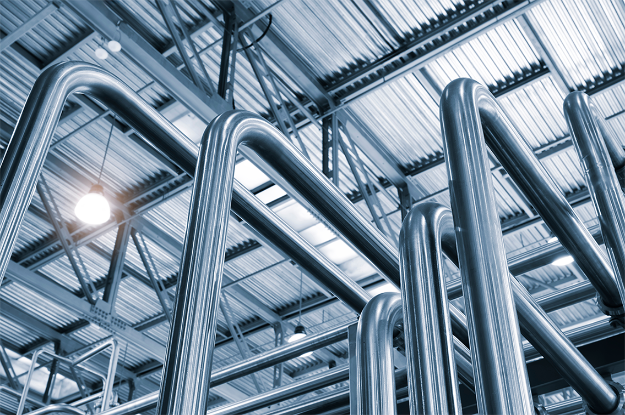
Power Generation
Do You Trust Your Process Analytics?
Accurate sampling all depends on regular maintenance. Are you maintaining the critical instruments that your plant relies on?
Read More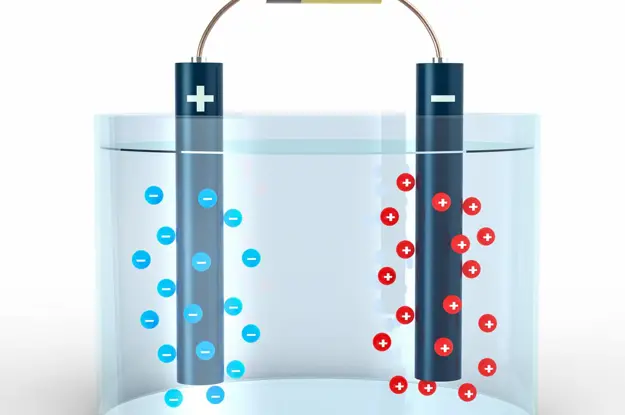
Power Generation
Cation Conductivity vs. Specific Conductivity
Conductivity is useful as a general measure of stream water quality. Each stream has a relatively constant range of conductivity. Once a baseline is established, it can be compared with regular conductivity measures.
Read More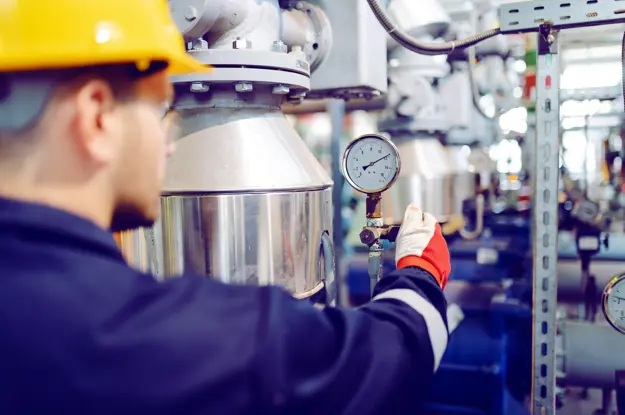
Power Generation
Monitoring Cooling Water Systems to Improve Plant Performance
Many plants within the manufacturing industry include processes where the product stream must be heated, cooled, or both to facilitate production. These plants often use heat exchangers or sample coolers with recirculating cooling water systems to do so.
Read More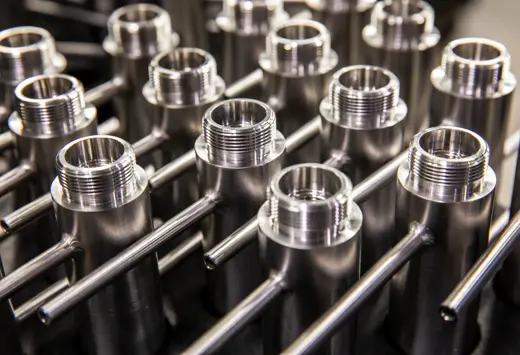
Protect Your SWAS
Sentry's sampling accessories ensure that you can maintain precise temperatures and/or pressures.