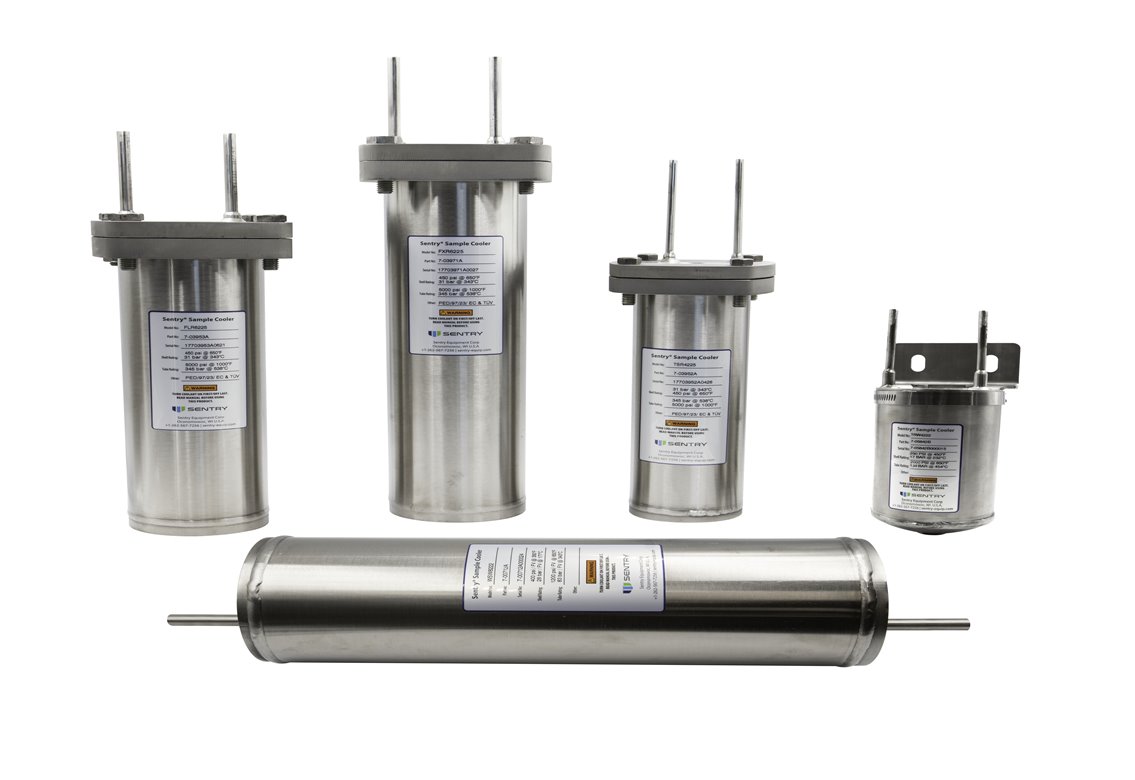
Sample Cooler Family
Plants and facilities of all kinds use sample coolers to cool a sample from a process stream.
Cooling samples as part of your steam and water sampling system is essential to maintaining safety and the representativeness of the sample.
For example, if a sample in a power plant is too hot to handle, the operator might throttle the flow to unacceptably low levels, which means the sample is no longer representative or acceptable.
Another example comes from Hydrocarbon processing or Process Analytics. Cooling the process to handle the sample is necessary. If you take a grab sample of a certain hydrocarbon whether it be of a liquid or a gas, the safest way is to handle the sample at below 140F. This protects the operator when handling hot samples that need to be physically taken to the lab safely for analysis.
In order to achieve accurate data, the Electric Power Research Institute (EPRI), ASTM and ASME recommend cooling water samples to 77°F (25°C) to ensure consistent, accurate test results.
HOW SAMPLE COOLERS WORK
A sample cooler is simply a small shell and coil heat exchanger that works like this:
- The sample to be cooled flows through the tube side of the cooler
- The cooling fluid, usually water, flows through the shell side to cool the temperature of the sample.
- The cooled sample is taken to a laboratory for analysis or piped to on-line process instrumentation for continuous monitoring of certain properties such as conductivity, pH or chemical constituent
3 TYPES OF COOLERS TO FIT YOUR NEEDS
There are several types of coolers designed for most applications in liquid, gas or steam processes.
1. Helical Coil – The most compact and highly efficient kind of sample coolers, these include a single continuous tube that’s helically coiled and fitted in a shell.
2. Spiral Tube – These coolers have a spirally coiled tube and manifold assembly fitted into a compact shell that optimizes heat transfer efficiency and space. The spiral shape of the coil and shell flow paths creates centrifugal force that enhances heat transfer on both sides in a true counterflow arrangement. They’re optimally designed for use with corrosive fluids and gases.
3. Tube-In-Tube DTC Series – These helically wound, full counter-flow heat exchangers are well-suited for a variety of applications where low flow rates of high-pressure and/or high-temperature fluids need heating or cooling.
CONSIDERATIONS NEEDED WHEN CHOOSING A SAMPLE COOLER
Adequate flow.
A truly representative sample requires adequate sample flow. Because of this, the sample cooler size will be determined by your samples’ required flow rate and the steam inlet pressure. For example, EPRI recommends a flow rate of 6 feet (1.8 m) per second on water samples. For steam samples, flow rates are lower due to the high velocity of the steam as it flows to the sample panel. Generally, flow rates of between 500-1,000cc per minute are adequate.
Two-stage cooling.
If the sample is to be fed to an in-line analyzer, rough cooling might not be sufficient. Some analyzers, particularly conductivity and pH, are very sensitive to temperature. To reach the recommended temperature of 77°F (25°C), two-stage cooling of the sample first rough cools the hot sample using plant cooling water, then uses mechanical refrigeration.
Installation.
Sample coolers can be mounted either vertically or horizontally, but it’s best to mount them vertically on high-temperature lines. Coolers are also typically installed with isolation valves in the cooling water piping to facilitate service.
Maintenance and service.
Most coolers need only occasional descaling of the shell side, which can be done chemically or mechanically after removing the shell.
When selecting the right sample cooler for your facility, it’s important to consider the requirements for each sample line to ensure adequate flow rates and optimize cooling water usage.
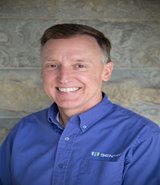
Written by Kevin Kirst
As industry manager for the refinery market, Kevin employs his 25-plus years of experience in engineering, application support, and sales to develop new ways to sample, monitor, and measure customers' processes, which the primary focus on the crude oil refining industry. Like all our company employee-owners, Kevin is committed to developing technologies and equipment that allow customers to operate their processes at optimal efficiency while maintaining high levels of safety and product quality.
Related Posts
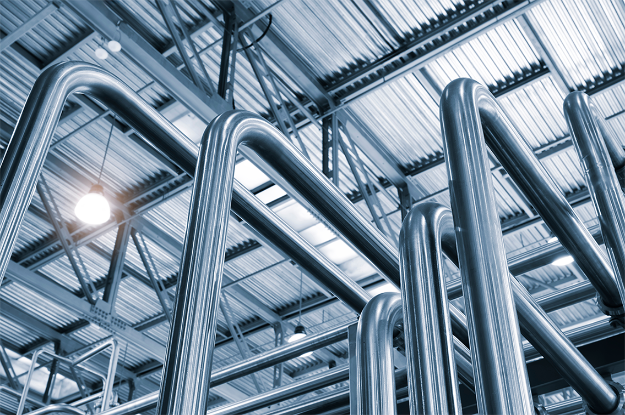
Power Generation
Do You Trust Your Process Analytics?
Accurate sampling all depends on regular maintenance. Are you maintaining the critical instruments that your plant relies on?
Read More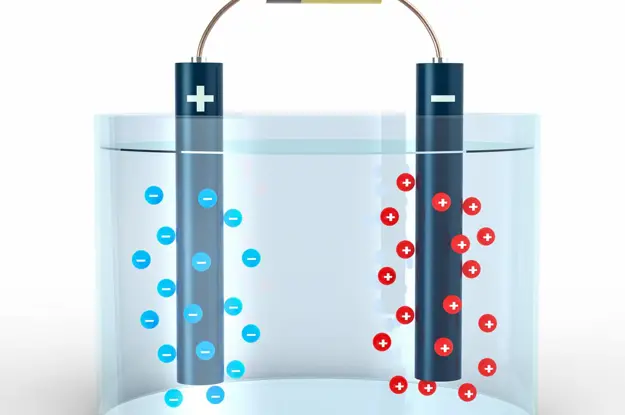
Power Generation
Cation Conductivity vs. Specific Conductivity
Conductivity is useful as a general measure of stream water quality. Each stream has a relatively constant range of conductivity. Once a baseline is established, it can be compared with regular conductivity measures.
Read More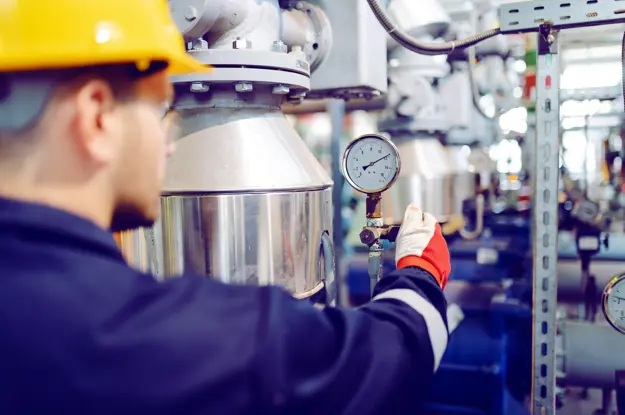
Power Generation
Monitoring Cooling Water Systems to Improve Plant Performance
Many plants within the manufacturing industry include processes where the product stream must be heated, cooled, or both to facilitate production. These plants often use heat exchangers or sample coolers with recirculating cooling water systems to do so.
Read More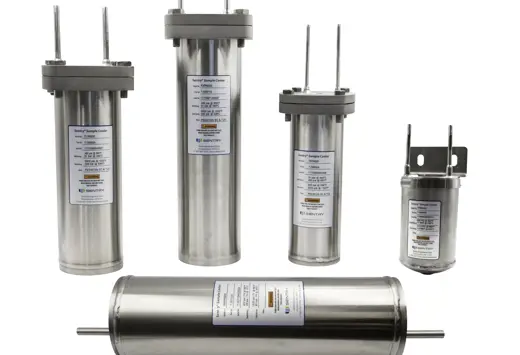
Protect Your SWAS
Protect your samples and equipment from high temperature events with Sentry's complete line of Sample Coolers.