Prepare Your Equipment for the Summer Heat with a Two-Stage Cooling Configuration
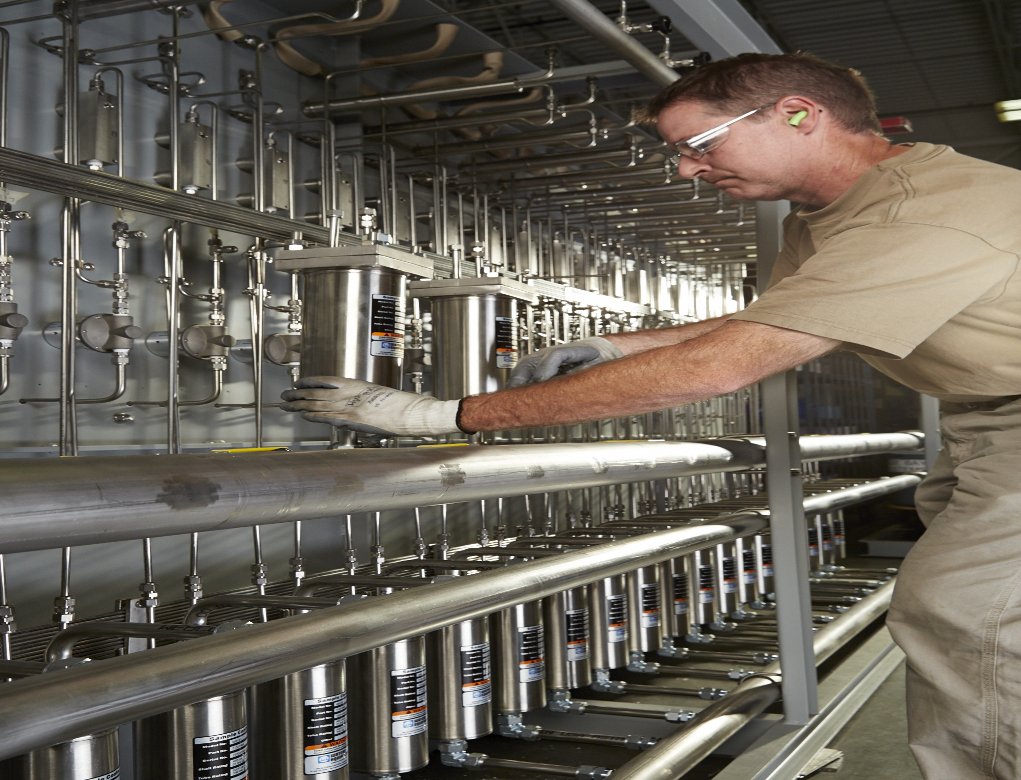
Avoiding extreme summer weather and even regular summer weather is not avoidable, and these conditions can cause havoc on steam and water analysis systems (SWAS) without adequate preparation.
The stress put on the equipment can come from a magnitude of effects, some including higher heat loads and increased cycling rates, in return increasing the risk of thermal issues and longer downtimes in your power plant. Before the summer months arrive, here are some simple solutions plant operators should consider.
The problem: Keeping the Temperature of Cooling Water
The sample cooler in a steam and water analysis system is essential to maintaining the safety, integrity, and representativeness of the sample . In the blog, Optimize Sample Cooler Temperatures for Ideal Results,” the cooling temperature for best results should be 77°F (25°C). With the extreme heat that summer can bring, maintaining this temperature becomes a larger challenge.
Sample coolers are designed to handle a variety of water temperatures and volumes based on application needs. These coolers are manufactured to cool water efficiently before it is tested for properties such as conductivity and pH. To cool a sample to the ideal temperature, the sample flows through the tube side of the cooler, and the cooling fluid flows through the shell side of the cooler. Once the sample is cooled, it is taken to a laboratory for analysis or piped to online process instrumentation for continuous monitoring of certain properties, including, conductivity, pH, or chemical constituents. This initial step is known as primary cooling.
As the environmental temperature rises, the cooling water temperature rises. In some cases, the temperature can increase by 40°F above the ideal temperature. As a result, the temperature of the sample significantly increases above its ideal temperature of 77°F, the standard analyzers must attempt to compensate high-temperature readings.
The Solution: A Two-Stage Cooling Process
As the EPRI standard states, the goal of a sample system is to “transport and condition a sample without altering the characteristics of interest. The system parameters which need to be controlled are velocity, pressure, and temperature.”
A secondary cooling configuration, or a two-stage cooling process is recommended by ASME and EPRI and is a necessity when higher temperatures render primary cooling insufficient. Data becomes more questionable and less repeatable the further away the cooling water and sample get from the 77°F standard without a secondary cooling configuration.
Most power generating plants already have a two-stage cooling process in place, but with aging plants, many rely on rough cooling. By introducing a secondary cooling configuration to a SWAS, the sampler is first cooled by using plant cooling water, then uses a closed loop of cooling water controlled by mechanical refrigeration. With that addition, the process provides backup during the summer months, ensuring the temperature increases do not compromise the samples integrity.
The Sentry Equipment team is here to help you find the solutions you need. Contact us at +1-262-567-7256, or complete our online contact form for more information.
This blog is adapted from an article contributed to POWER Magazine by Sentry Equipment.
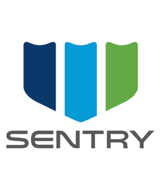
Written by Sentry Equipment
With proven sampling expertise since 1924, Sentry products and services provide business operations the critical insights to optimize process control and product quality. We deliver true representative sampling and analysis techniques to customers around the globe, empowering them to accurately monitor and measure processes for improved production efficiency, output and safety. Standing behind our commitments, we are determined to tackle any application, anywhere.
Related Posts
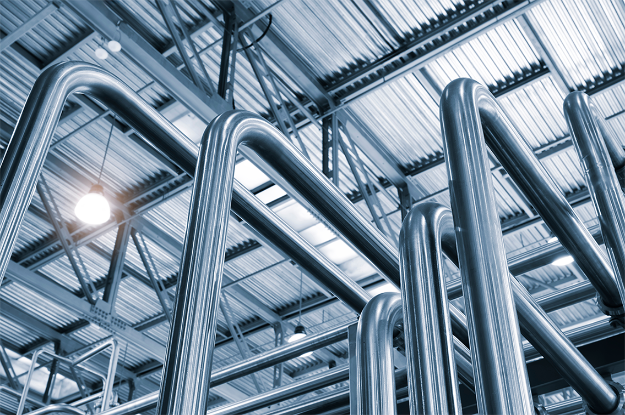
Power Generation
Do You Trust Your Process Analytics?
Accurate sampling all depends on regular maintenance. Are you maintaining the critical instruments that your plant relies on?
Read More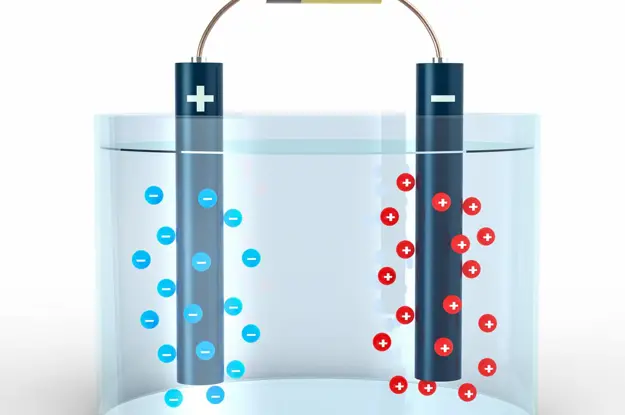
Power Generation
Cation Conductivity vs. Specific Conductivity
Conductivity is useful as a general measure of stream water quality. Each stream has a relatively constant range of conductivity. Once a baseline is established, it can be compared with regular conductivity measures.
Read More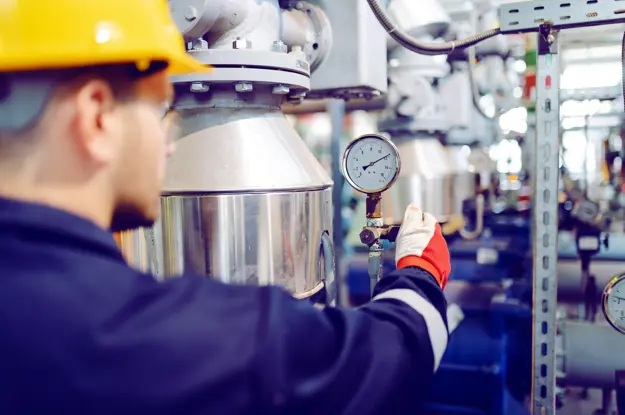
Power Generation
Monitoring Cooling Water Systems to Improve Plant Performance
Many plants within the manufacturing industry include processes where the product stream must be heated, cooled, or both to facilitate production. These plants often use heat exchangers or sample coolers with recirculating cooling water systems to do so.
Read More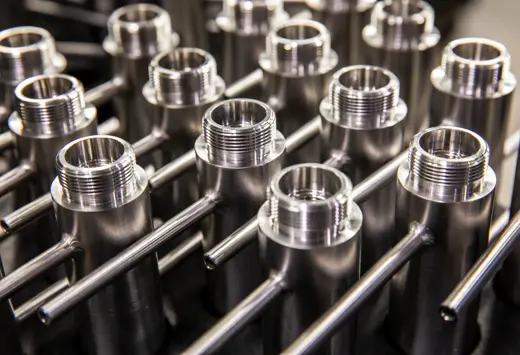
Protect Your SWAS
Sentry's sampling accessories ensure that you can maintain precise temperatures and/or pressures.