Tips for Managing Steam and Water Analysis System Maintenance in Aging Plants
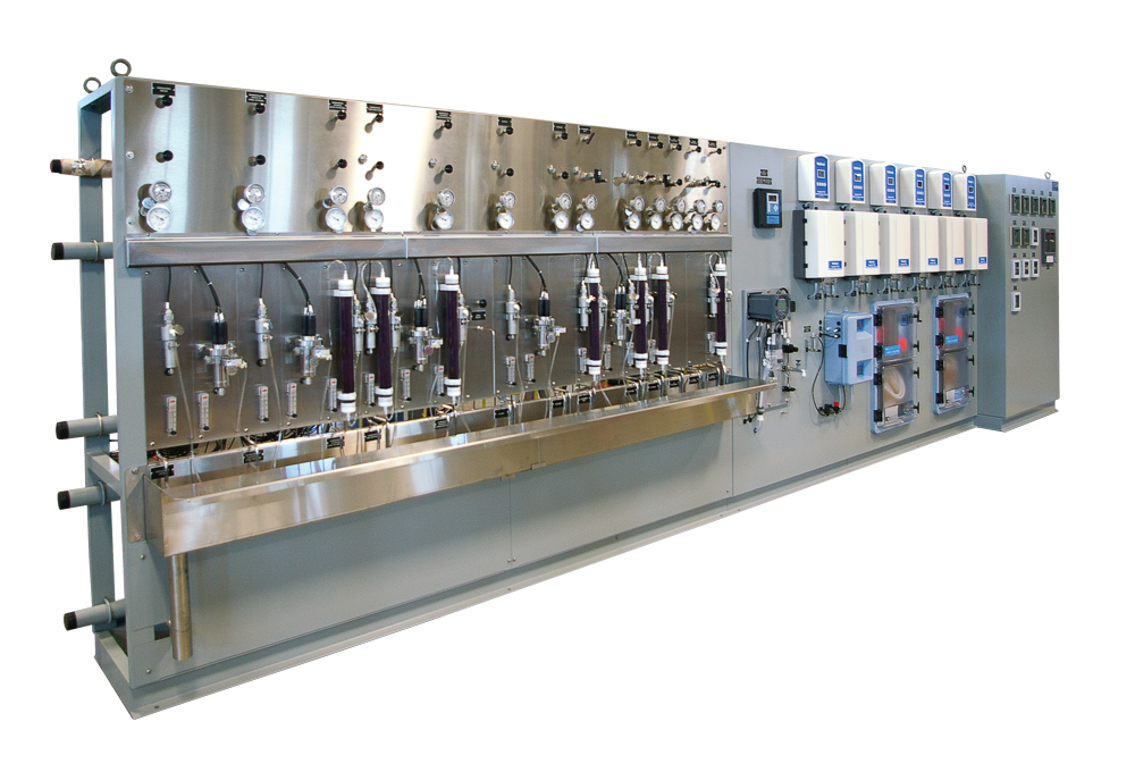
Proper SWAS maintenance is critical to the operation of any plant. Managing the water chemistry is crucial to ensuring piping integrity and process efficiency.
This blog is adapted from a January 2024 article written by Jeff McKinney, Sentry Equipment's regional manager for utilities, for POWER Magazine.
Proper steam and water analysis system (SWAS) maintenance is critical to the operation of any coal, nuclear, or combined cycle power plant, many of which are being forced to ask more of aging equipment. Due to the critical role water plays in power generation, managing water chemistry is crucial to ensuring piping integrity and process efficiency. Foundational in water chemistry management is the maintenance of an effective SWAS that is properly and carefully monitored.
For plants looking to avoid total system replacement, there are several solutions available to extend the lifecycle and improve efficiency of aging equipment.
SWAS Challenges in Power Plants
The most significant risk of an improperly maintained SWAS is that improper flows and poorly maintained analyzers can leave the plant essentially running blind. A malfunctioning SWAS leaves steam turbines more vulnerable to chemistry excursions, which can cause forced plant outages and loss of plant efficiency. The most common SWAS performance issues stem from prolonged periods without proper maintenance, and the consequences of failing to prioritize equipment maintenance can be catastrophic.
Plant Cycling, Corrosion, and Erosion. Commercial power plants weren’t specifically designed for cycling and varying plant loads. Cycling creates thermal and mechanical stresses that disrupt the protective layer on the boiler tubing and key components, gradually breaking down and eroding the equipment. These plants are left particularly vulnerable to the corrosion and erosion of their equipment.
Excessive Magnetite Buildup and Fouling. Cycling can cause increased migration of magnetite and hematite from plant piping. These particulates can infiltrate the sampling system, which can cause irregular pressure drops, flow suppression, and equipment damage – stockpiling the number of downstream maintenance issues. If not addressed, magnetite can wreak further havoc within a plant’s SWAS by plugging sample conditioning components and analyzers.
Solutions for Aging Systems
Cost-effective maintenance solutions are available for all plant operators, including those with a SWAS at the end of their lifecycle that don’t have the budget for a complete replacement.
Magnetic Traps. Magnetic traps use high-strength magnets to isolate and capture corrosion products, like magnetite particulates, from the sample stream to protect sample conditioning and analytical instruments from critical downtime and costly repairs.
Magnetic traps are highly recommended for any plant that cycles, as they prevent plugged lines and preserve proper flows to downstream components. The magnetic trap is typically located upstream of the pressure control valve, where most particulate lodges. They help improve flow consistency for cycling plants and the reliability of downstream components, such as thermal shutoff devices that can be negatively affected by magnetite. If improperly cleaned or maintained, magnetic traps simply become “loaded,” meaning they can’t attract additional magnetite until the particulates are flushed out. To solve this issue, magnetic traps are equipped with a flush handle that easily purges the trapped material from the line.
Magnetic traps are commercially available for use in both low- and high-pressure applications, protecting both the sample conditioning equipment and the analyzers. They’re easily retrofitted into most existing SWAS.
Magnetic traps are an extremely popular, low-maintenance solution for managing corrosion product buildup.
High-Pressure Blowdown Valves (HPBVs). From the point of extraction all the way through the panel, HPBVs can purge any contaminants from the line to keep sample lines clear. HPBVs are located between the sample line and a blowdown header that’s routed to a drain or tank arrangement prior to temperature or pressure reduction. While effective, retrofitting a high-pressure blowdown header to an existing panel is more involved than adding magnetic traps.
Corrosion Product Samplers. The American Society for Testing and Materials (ASTM) guidelines recommend using corrosion product samplers for collecting and quantifying corrosion products.
These samplers collect particulate and ionic matter circulating in the secondary piping of nuclear power plants and condensate/feedwater systems of fossil-fueled plants. For example, the Sentry CPS Sampler is a portable, standalone unit that collects sample material on filters that are later removed for laboratory analysis. The data from a comprehensive corrosion monitoring program can be utilized to assist plant chemists in optimizing their chemistry program including identifying component specific metal loss.
Get an expert Opinion
It can be difficult- and even dangerous- to pinpoint a problem's cause within a SWAS. Contacting a qualified vendor that specializes in sampling retrofitting, replacement, and sample panel and analyzer maintenance services gives you the opportunity to discover where a system is in its lifecycle and what solutions can prolong it.
Sentry can help you diagnose and correct any issues in your SWAS. Contact us at +1-262-567-7756, or complete our online contact us form for more information.
You can read the entire online article here.
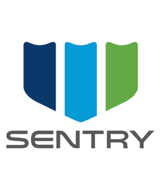
Written by Sentry Equipment
With proven sampling expertise since 1924, Sentry products and services provide business operations the critical insights to optimize process control and product quality. We deliver true representative sampling and analysis techniques to customers around the globe, empowering them to accurately monitor and measure processes for improved production efficiency, output and safety. Standing behind our commitments, we are determined to tackle any application, anywhere.
Related Posts
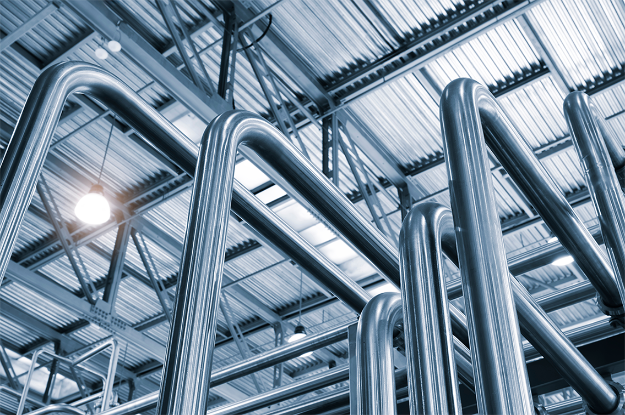
Power Generation
Do You Trust Your Process Analytics?
Accurate sampling all depends on regular maintenance. Are you maintaining the critical instruments that your plant relies on?
Read More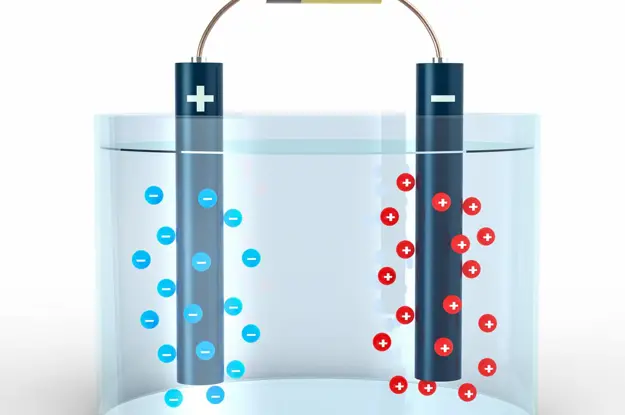
Power Generation
Cation Conductivity vs. Specific Conductivity
Conductivity is useful as a general measure of stream water quality. Each stream has a relatively constant range of conductivity. Once a baseline is established, it can be compared with regular conductivity measures.
Read More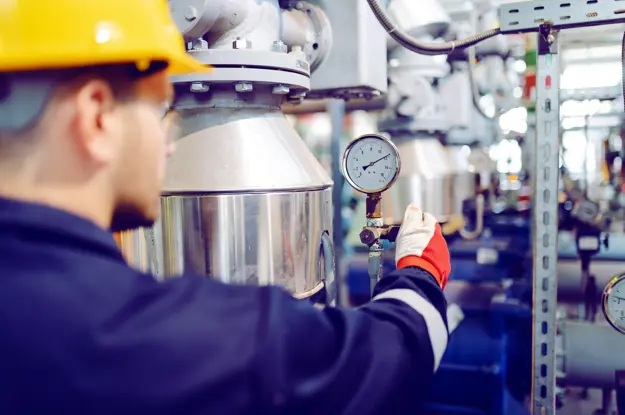
Power Generation
Monitoring Cooling Water Systems to Improve Plant Performance
Many plants within the manufacturing industry include processes where the product stream must be heated, cooled, or both to facilitate production. These plants often use heat exchangers or sample coolers with recirculating cooling water systems to do so.
Read More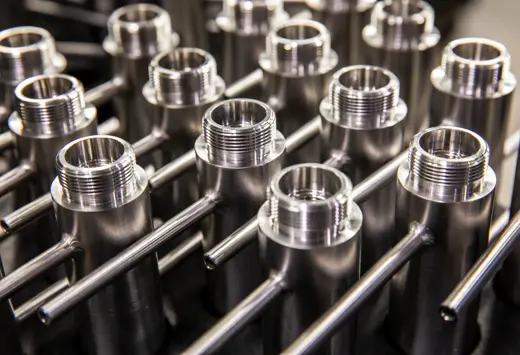
Protect Your SWAS
Sentry's sampling accessories ensure that you can maintain precise temperatures and/or pressures.