Beat Corrosion Every Step of the Way in Wastewater Treatment Plants
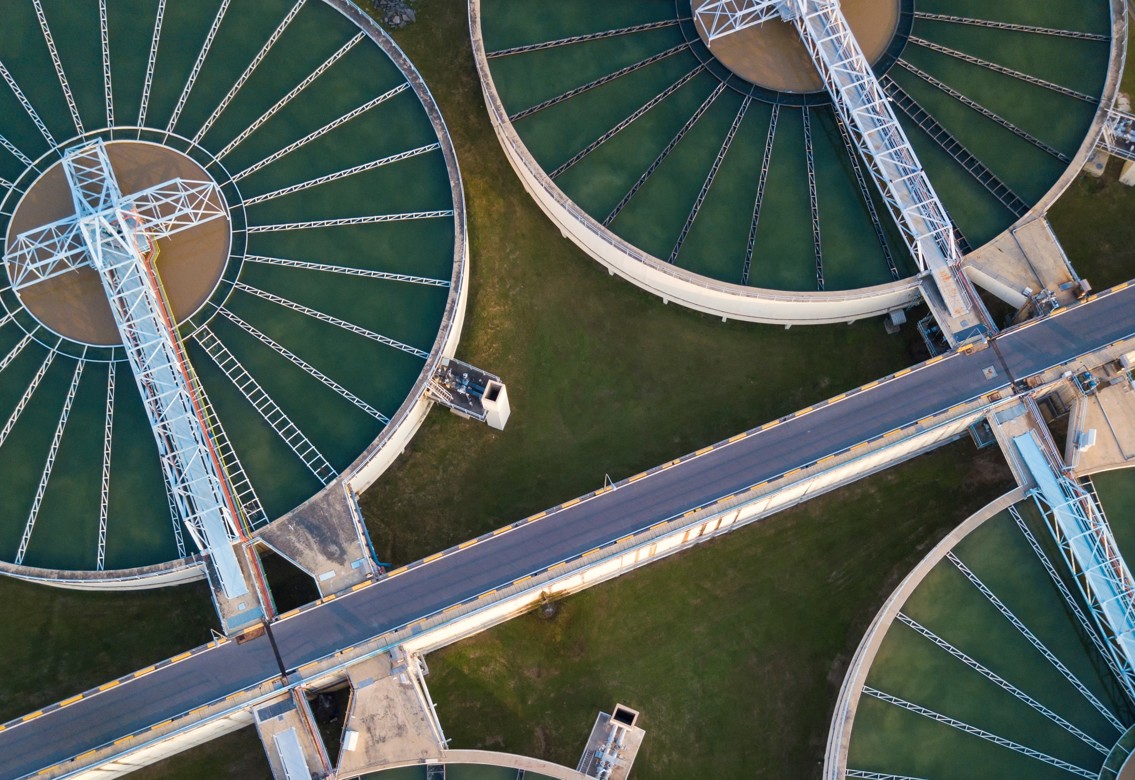
In wastewater treatment facilities, water + metal + oxygen = corrosion.
It’s an inevitable natural process that threatens the structural integrity and operating efficiency of equipment. Although it’s impossible to completely prevent corrosion, understanding how it happens and how to slow its spread can exponentially extend the life span of wastewater treatment equipment.
Sources of Corrosion
pH Levels. Water’s pH level is a measurement of the activity of free hydrogen and hydroxyl ions in a solution, which is measured on a scale of 0 to 14. In acidic conditions (a pH level below 7), certain metals like iron, steel and copper are more prone to corrosion. In highly alkaline environments (pH above 7), corrosion can affect materials such as aluminum and some stainless steels.
Weather. Some weather conditions, such as humidity, can influence local pH levels and leave equipment susceptible to rapid corrosion. According to experts, wastewater treatment facilities that experience high rates of corrosion should consider installing stainless steel equipment, as opposed to steel, due to its chromium content.
Water Conductivity. When metals are exposed to water with high electrical conductivity, dissolved ions can move more freely. Corrosion involves electrochemical processes, where metals lose electrons, leading to oxidation. This process can occur more rapidly in a conductive environment because ions can easily transfer between the metal surface and the surrounding solution.
Galvanic Corrosion
Wastewater treatment facilities are most susceptible to galvanic corrosion, which occurs when one metal is in electrical contact with another metal in a conducting corrosive environment. Because wastewater treatment facilities are filled with metal equipment like pumps, valves, drives and skimmers, structural steel treatment tanks are prime breeding grounds for corrosion. Although it can manifest anywhere, there are certain parts of the tank that have a higher probability for galvanic corrosion than other areas in the tank.
Clarifiers. The highest corrosion risk is the point near the top of the clarifier where air and water meet. The combination of constantly moving metal and oxidation rapidly increases the rate of corrosion. Without proper maintenance, clarifiers could fail at a moment’s notice. To help reduce the rate of corrosion, plant managers should look for clarifiers manufactured with corrosion-resistant metals, such as stainless steel and aluminum, and/or are treated with corrosion-resistant coatings.
Skimming devices. Another corrosion hot spot is where the skimming device attaches to the metal on the feedwell. Again, the constantly moving metal increases the rate of galvanic corrosion and can lead to clarifier failure.
Proactive inspections and maintenance – especially on equipment known to be susceptible to corrosion – can prevent equipment downtime and plant shutdowns, saving wastewater treatment plants thousands of dollars in fines and repairs.
The Solution: Repair & Retrofitting
When equipment becomes corroded, plant managers don’t have to spend the time and money to purchase new equipment. Choosing repair and retrofit services is often a less expensive and more effective solution.
Repairing and retrofitting cost-effectively reinstates equipment to its previous state – and sometimes even better functionality. Through improvements like corrosion-resistant coatings, improved welding integrity and technology upgrades, retrofit services can help plants maintain their original infrastructure, leading to fewer complications and compatibility issues.
Sentry offers holistic services to help you prevent corrosion in your wastewater treatment equipment. Our repair and retrofit services can help you efficiently manage corroded equipment. Contact us at +1-262-567-7256, or complete our online contact form for more information.
See the full article on Pumps and Systems.
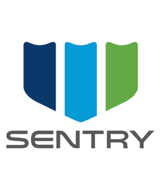
Written by Sentry Equipment
With proven sampling expertise since 1924, Sentry products and services provide business operations the critical insights to optimize process control and product quality. We deliver true representative sampling and analysis techniques to customers around the globe, empowering them to accurately monitor and measure processes for improved production efficiency, output and safety. Standing behind our commitments, we are determined to tackle any application, anywhere.
Related Posts
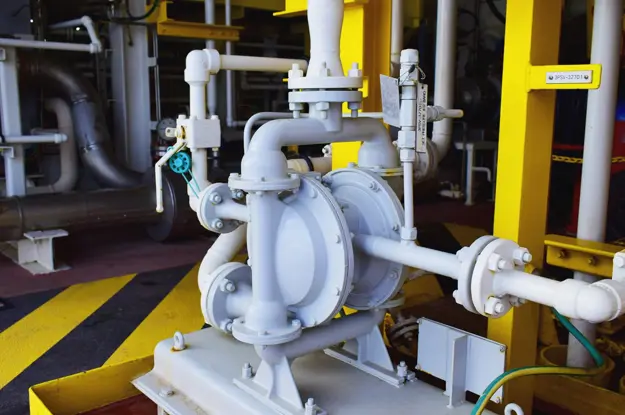
Water/Wastewater
Why Do I Need a Diaphragm Pump?
What is a Diaphragm Pump? Designed by Dorr Oliver, the ODS Diaphragm Pump transfers slurry materials evenly and simply utilizing air. Each of these pumps can be automated to match your processing capacity to see maximum efficiency.
Read More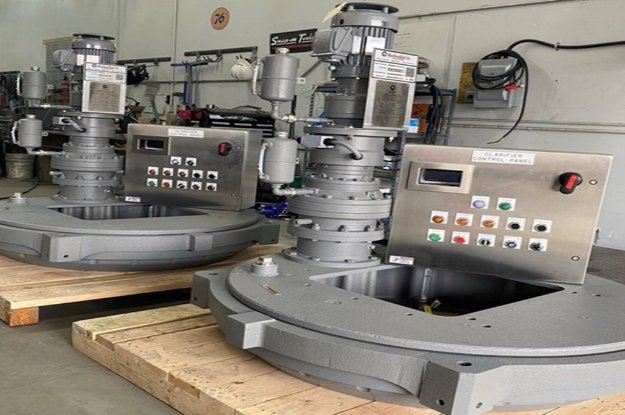
Water/Wastewater
Repair vs. Replace Your Clarifier Drive
A clarifier drive unit supplies torque to rotate the rake arms through wastewater. Clarifier drives must be replaced or repaired over time for many reasons. Rebuild-it, a Sentry Equipment Service, has water and wastewater solutions to meet your needs and prevent downtime.
Read More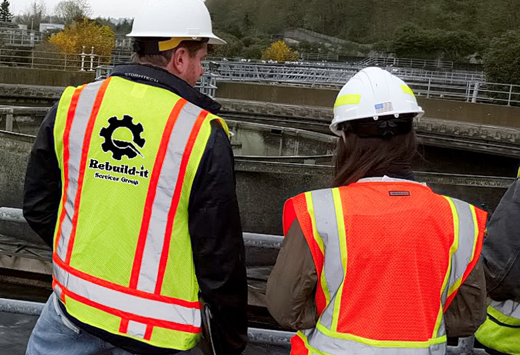