Ask Sentry: What Is Cation Conductivity and Why Is It Important?
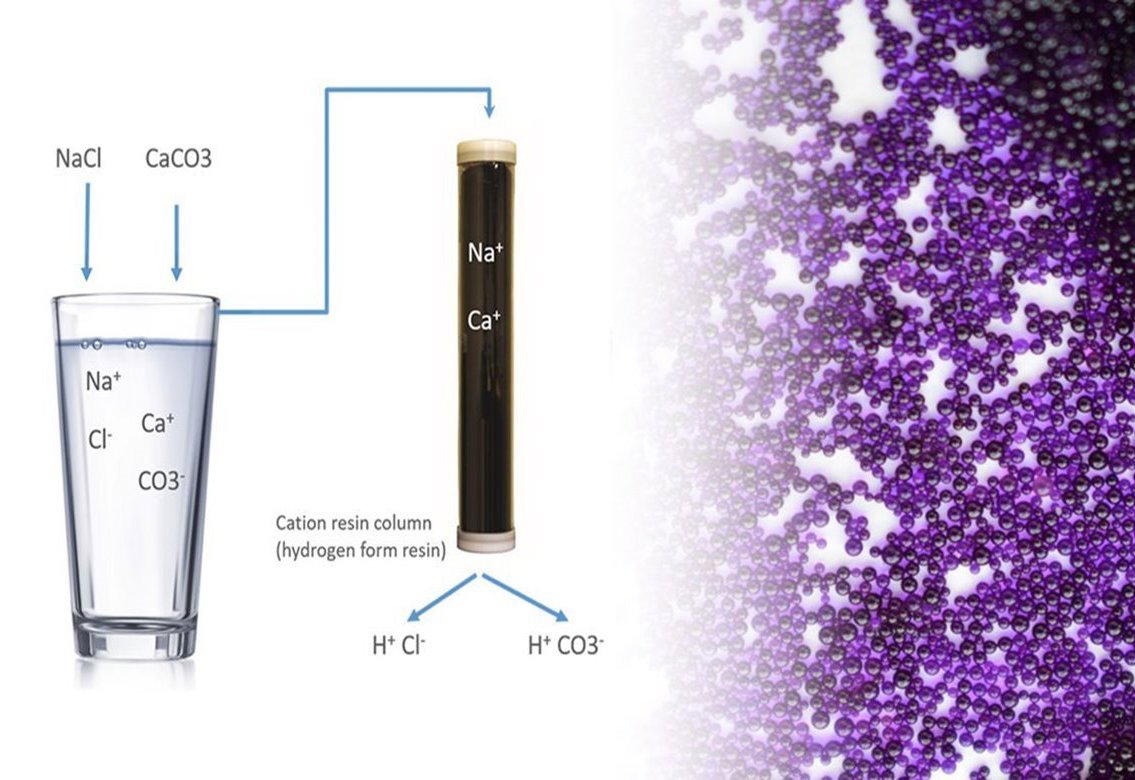
Cation Conductivity
In the utility industry, cation conductivity measurements help plants identify minor problems so plant personnel can remedy the issues before they become major complications.
The Shield sat down with John Powalisz, Sentry Equipment's Director of Business Development, to discuss what cation conducivity is, challenges plants often face with cation conductivity and how to solve these issues.
The Shield (TS): What is cation conductivity, and how does it work?
John Powalisz (JP): Cation conductivity is one of the best ways to monitor for contaminants within a steam or water sample. It is also referred to as Conductivity after Ion Exchange (CACE), Acid Conductivity and After Exchange Conductivity.
Ionic “species” or ions are present in a sample stream because compounds break down (dissolve) in water. High process temperatures accelerate this process. Other measurements are used to identify other contaminants in the system.
These ions can be positively charged (cations) – including sodium, copper, iron, manganese and hydrogen – and negatively charged (anions), like chlorides and sulfates which are of particular concern as they are sources of corrosion. Cation conductivity separates the positively charged ions from the process stream in a cation resin column.
As an example, in a power plant, we wish to identify contaminants like salts that might be present as a result of a condenser tube leak. The salt will dissolve and create NA+ and Cl-. The cation resin will capture the positively charged Sodium ions, displace a positively charged hydrogen ion which will bond with the negatively charged chloride ion creating HCL and increasing the conductivity measurement value thereby indicating a contaminant is present.
TS: Why is cation conductivity significant in a utility plant?
JP: Cation conductivity prevents contaminants from causing more significant issues in the plant.
For example, when sodium chloride enters a turbine and forms a deposit on the turbine blades and that turbine is later shut down without any dry-air protection, the combination of sodium chloride deposit, oxygen In the air and moisture allow the chloride ion to become highly corrosive and form pits on the turbine blade surfaces. Over time these pits can lead to catastrophic failures.
In high-pressure boilers (10 Mpag, 1450 psig and above) sodium chloride contamination can lead to aggressive corrosion of the boiler tubes leading to hydrogen embrittlement failures in the water walls. Cation conductivity can catch this problem early to maximize clean water in a plant’s processes and minimize downtime.
TS: What are cation resin columns?
JP: Cation resin columns exchange cations for anions by using negatively charged plastic beads to capture positively charged ions in a solution.
The positively charged cations bind to functional groups on the plastic beads, replacing a hydrogen ion which is released. The released hydrogen ions can create an acidic solution – that’s why cation conductivity is sometimes called acid conductivity or Conductivity after Cation Exchange (CACE). Cation resin columns are highly sensitive to contaminants and can detect low levels of them.
The length to diameter ratio of the non-reactive plastic column is important to ensure proper flow, residence time and volume of resin.
Most cation exchange resin includes a color indicator such that when the resin is exhausted (unable to exchange ions) it changes color, different resin manufacturers use different color indicator dyes most commonly deep purple or dark red, and change to light brown and light red, respectively, when exhausted.
The color change happens sequentially until all the resin is exhausted.
When all the resin in the column has changed color, the resin can no longer remove any cations and they can exit the column which increases the conductivity on the outlet. The resin should now be replaced with fresh resin or regenerated resin.
TS: What applications are cation resin columns used with?
JP: Cation resin columns can be helpful in several applications, including:
- Spotting iron which is due to corrosion of the power plant
- Detecting minerals and mineral salts/acid contaminants
- Detecting sodium, typically from cooling system leaks which can damage equipment quickly
- Identifying leaks that can introduce contaminants to the process
- Detecting compounds carried over in the steam from the boiler
TS: What challenges do utility plants often face with cation conductivity?
JP: Sometimes plants use poorly designed or oversized cation exchange cartridges with the misguided belief that they will extend service life. However, this can result in suboptimal exchange rates, poor resin kinetics, leaching and can lead to inaccurate measurements.
In addition to using the correct ion exchange column, good quality resin and replacing or regenerating the resin when exhausted, sample temperature can adversely affect cation conductivity measurements.
For example, conductivity is highly temperature-sensitive, so the sample temperature mustn’t be too hot. These issues are prevented by using high-quality resin, conducting regular maintenance, and carefully controlling the sample flow and temperature. Don’t just rely on an instrument’s built-in temperature compensation, validate it in your operating conditions.
Consider using secondary sample cooling to remove temperature bias and improve measurement stability.
TS: How can utility plants ensure a successful cation conductivity program?
JP: Ensure you utilize the appropriate cation resin column size to deliver the runtime you require and that your measurement sensor is accurate at flow rates compatible with conductivity sensors, usually about 100 to 200 cc per minute.
Additionally, assure you are up-to-date on the latest guidelines and best practices from EPRI, IAPWS and ASTM. If needed, you can pull in an expert partner to ensure your measurements are accurate and dependable.
Benchmark your analytic system to EPRI and IAPWS guidance on minimum core instrumentation for your plant type, chemistry and operating parameters. Consider augmenting the system with Smart Chemistry Alarms for improved confidence in measurements.
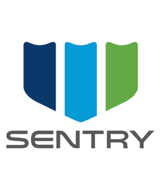
Written by Sentry Equipment
With proven sampling expertise since 1924, Sentry products and services provide business operations the critical insights to optimize process control and product quality. We deliver true representative sampling and analysis techniques to customers around the globe, empowering them to accurately monitor and measure processes for improved production efficiency, output and safety. Standing behind our commitments, we are determined to tackle any application, anywhere.
Related Posts
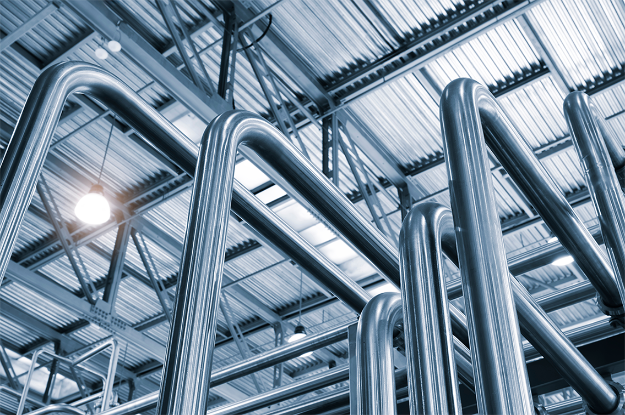
Power Generation
Do You Trust Your Process Analytics?
Accurate sampling all depends on regular maintenance. Are you maintaining the critical instruments that your plant relies on?
Read More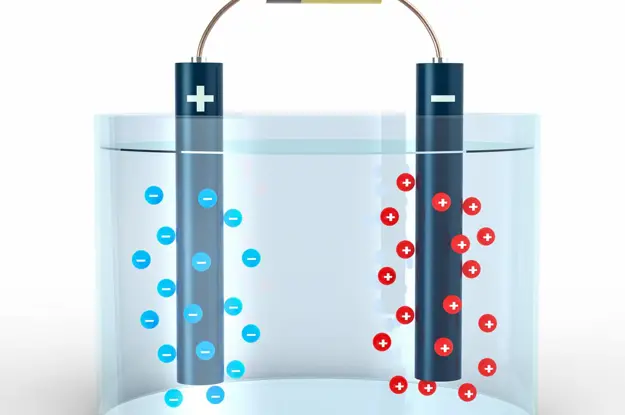
Power Generation
Cation Conductivity vs. Specific Conductivity
Conductivity is useful as a general measure of stream water quality. Each stream has a relatively constant range of conductivity. Once a baseline is established, it can be compared with regular conductivity measures.
Read More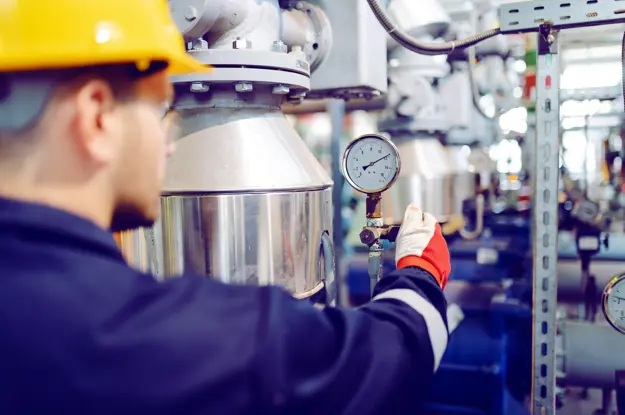
Power Generation
Monitoring Cooling Water Systems to Improve Plant Performance
Many plants within the manufacturing industry include processes where the product stream must be heated, cooled, or both to facilitate production. These plants often use heat exchangers or sample coolers with recirculating cooling water systems to do so.
Read More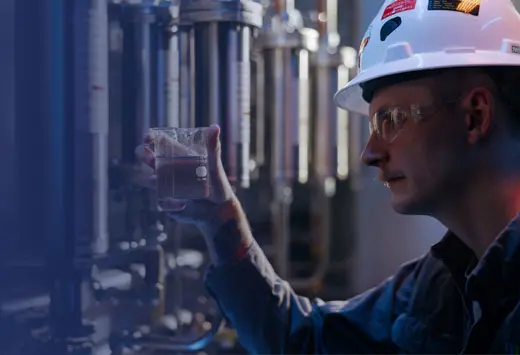
Maintain Water Sample Accuracy
Confirm your chemistry decisions with Sentry Equipment’s complete line of temperature, pressure, and regulation equipment.