Avoid a Pipeline Freeze with a Methanol Injection Plan
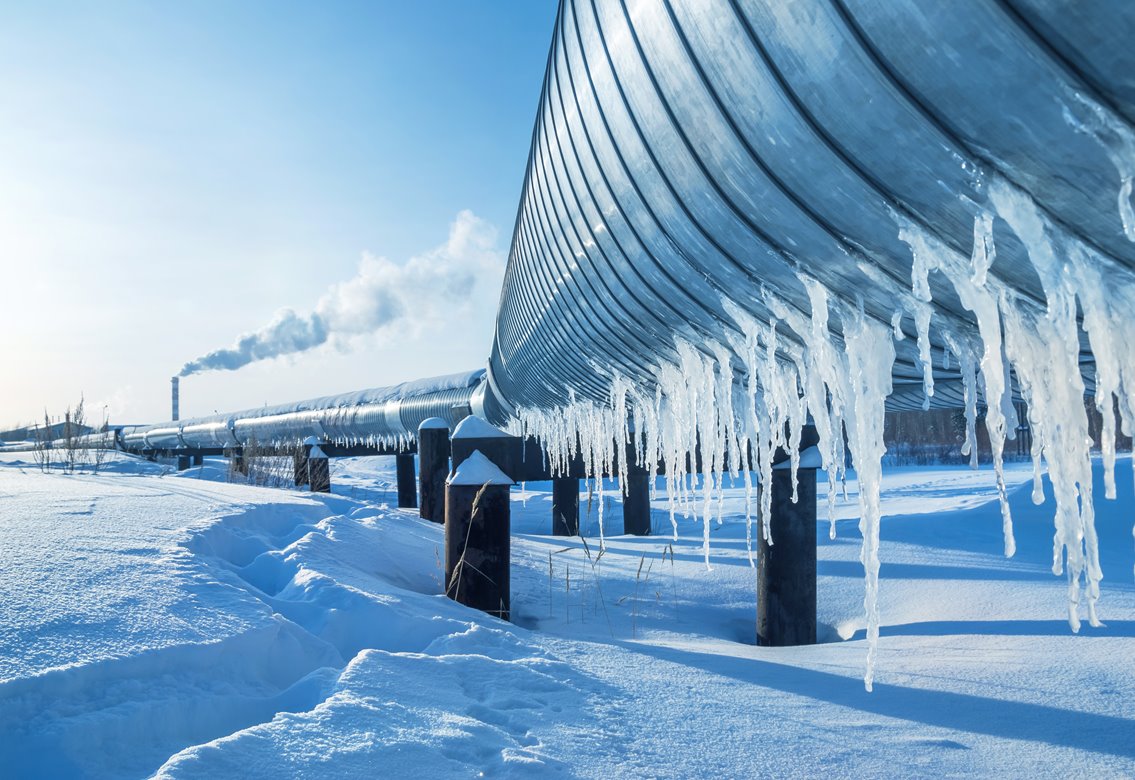
As temperatures drop, equipments risk of damage increases.
As temperatures drop, the risk of freezing becomes more likely in pipelines, leading to flow blockages and may cause system damage. Companies are required by strict federal and local regulations to maintain secure operations and prevent pipeline freezes. Due to these regulations, many companies have implemented a Methanol injection plan to ensure maximum uptime and decrease the risk if damaged equipment.
Methanol (MeOH) is widely used in the oil and gas industry to act as an inhibitor in natural gas pipelines, usually in colder climate facilities. Methanol works as an antifreeze by lowering the freezing point of water and water-based liquids that make their way into pipelines or reservoirs. The practice of menthol injection is the most economical solution for preventing hydrate formation- the formation that occurs due to the reaction of water with hydrocarbons.
Operators can inject Methanol in two ways. The most common is due to the practice being the most economical and efficient with injection through standard check valves into gas pipelines. Ideally, injecting methanol through atomization will increase the dispersion efficiency, reduce usage and decrease corrosion rates caused by oxygen-laden methanol.
Creating an effective Methanol Injection Plan
First, there are some questions to consider before choosing Methanol injection:
- Did we have freezing issues last year that needs to be addressed this year?
- How do we currently inject Methanol?
- Is the rate we inject Methanol rising to keep our pipelines from freezing?
- Do we over-inject Methanol to ensure our pipelines are not freezing?
These questions will help your decision in creating a Methanol injection plan or reassess your existing plan.
Chemical pump selection
Under-injecting your lines creates the chance for your pipeline to freeze, and over-injecting is a leading cause to corrosion and is a waste of valuable chemicals.
There are three pump options to choose from; however, it is critical to select the correct size. Whether you choose electric, solar, or pneumatic, it must fit your needs of pressure, volume, and injection method and ensure the seals are compatible with Methanol.
Implement a controller
A controller may prevent damage to your equipment with its ability to deliver automatic chemical injections. Most chemical pump companies now provide controllers to ease the mind of the user as it ensures accurate chemical dispersal at the right time. Most controllers have ambient temperature settings that can be set to activate when temperatures drop to a set number and stop injection when temperatures rise to the set number your equipment needs.
Other applications include a timer that can be used to atomize the process on set cycles instead of the standard continuous method. This allows extremely low rates to be used with optimal dispersion.
Optimizing the injection
The correct atomizer for the target helps you significantly reduce Methanol feed rates by optimizing the dispersal of your Methanol. These atomizers utilize the gas velocity to aid in coverage. Depending on the rate of injection, the cost of adding an atomizer can be saved in Methanol costs in an average of 60 days (about 2 months) or less.
Identify the injection location
The effectiveness of any chemical injection, including atomization of Methanol, depends on the location of the injection point. Choosing the optimal injection method and injection point is just as crucial as selecting the correct chemical.
The Sentry Equipment team has over 200 years of experience, with more than 35 years in experience with preventing internal corrosion and implementing chemical injection systems. Our experts are here to help you. Contact us at +1-262-567-7256 or complete our online contact us form for more information.

Written by Bryan Stockburger
From chemical application to pipeline corrosion, Bryan Stockburger brings over 14 years of experience to midstream/downstream companies as a regional sales manager for Sentry Equipment. Bryan works extensively with field operations throughout the US and has obtained multiple safety certifications from producers, chemical providers and vendors.
Related Posts
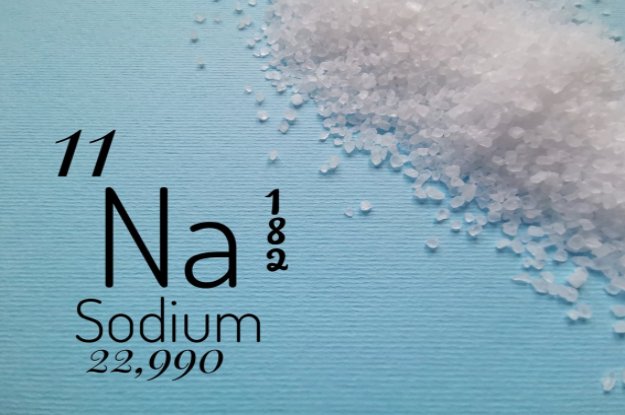
Preventative Maintenance
Monitoring Sodium in Power Plants
An increase in sodium measurements may identify unwanted dissolved impurities. When coated on the boiler turbine blades and heat exchanger surfaces, these impurities can cause catastrophic problems in power plants.
Read More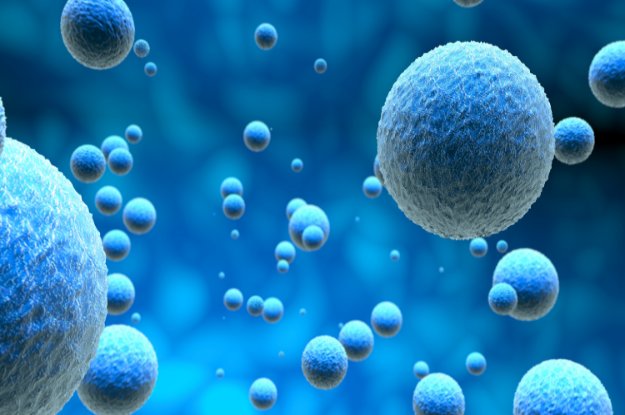
Preventative Maintenance
The Advantages of Chlorine Dosing to Control Biofilm in Industrial Cooling Systems
Microorganisms are organisms of microscopic size, which may exist in its single-celled form or as a colony of cells such as bacteria, fungi, and algae.
Read More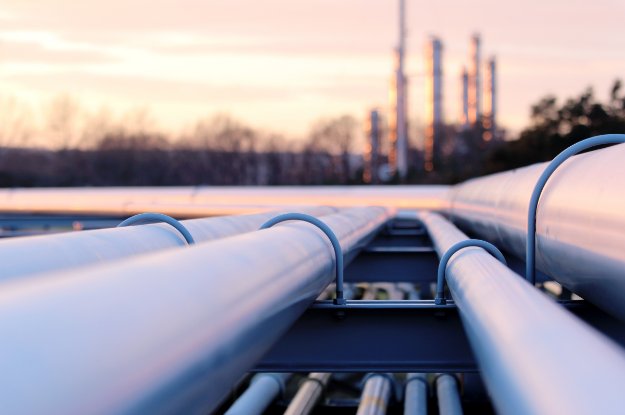
Preventative Maintenance
CASE STUDY: Prevent Equipment Downtime due to Crude Oil Leaks
A G50 Crude Oil pipe may cause significant damage to machining operations, equipment, and employee safety within a facility.
Read More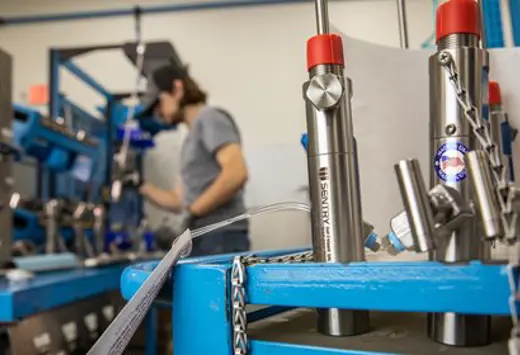
Mitigate Pipeline Freeze
Sentry's complete line of atomizers can help you protect your pipelines from impending freeze.