The Advantages of Chlorine Dosing to Control Biofilm in Industrial Cooling Systems
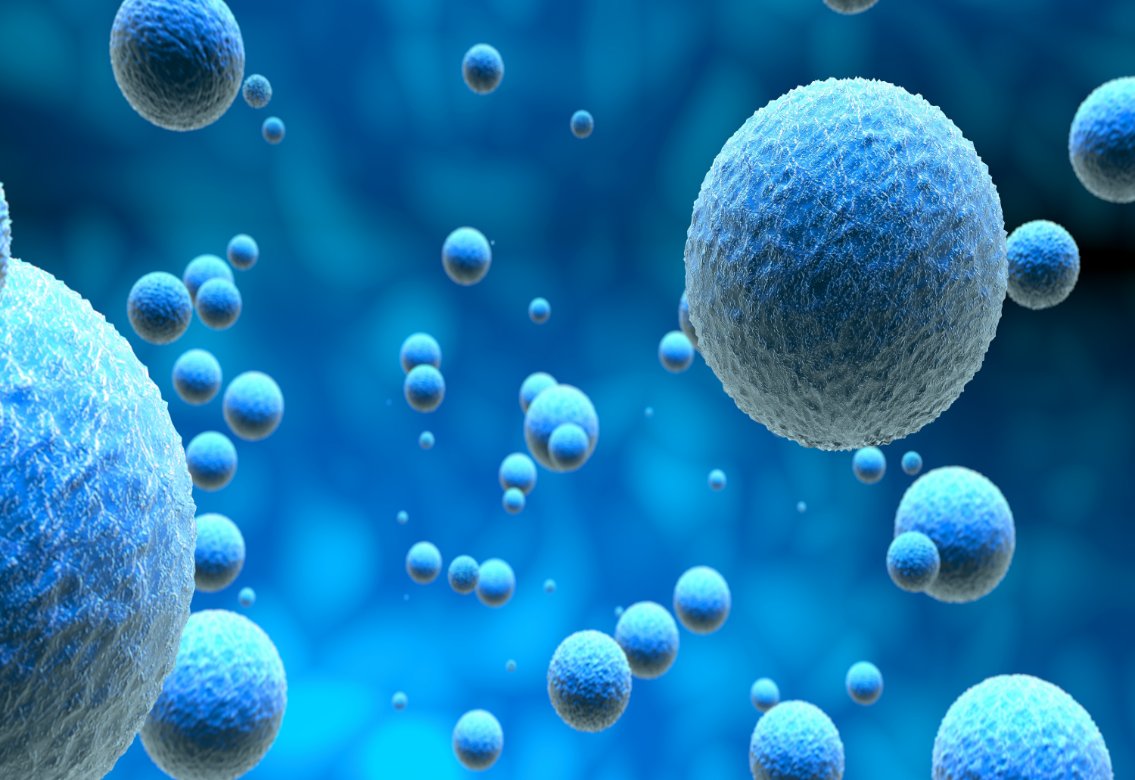
Microorganisms are organisms of microscopic size, which may exist in its single-celled form or as a colony of cells such as bacteria, fungi, and algae.
These microorganisms can present challenges in maintaining and operating industrial cooling systems. Contaminants can increase pathogens and create biofilms (a community of microorganisms) in cooling systems. This biofilm can lead to equipment damage and inaccurate measurements. One way to combat these concerns is through chlorine dosing.
One of the most common chemicals used to control biofilm in industrial cooling systems is liquid sodium hypochlorite (chlorine bleach.) Plants use this chemical to remove this film to encourage:
- Optimum equipment performance
- Maximized economic performance
- Operator safety
- Environmental protection
Limiting microorganisms with chlorine doing:
Typically, chlorine bleach is introduced into the water of a cooling system in liquid form. This forms several free compounds, including hypochlorous acid (HOC1) and hypochlorite (OC1-), that help control microorganisms. The percentage of these compounds created is based on the pH of the water, so pH is often closely monitored.
However, low-level doses of chlorine might not be enough to control microorganism growth within cooling water systems. When chlorine is added to cooling water systems, any free residual will quickly dissipate once the feed is discontinued. This allows the biofilm populations to recover quickly. For example, one bacterium with a generation time of 30 minutes will generate a population of 28,147,497,660,000 bacteria in just 24 hours. To combat this residual generation, adding controlled residual spikes of chlorine is recommended for a more effective chlorination program.
Best Practices for Chlorine Delivery
Chlorine must be continuously fed, carefully monitored and precisely controlled through real-time, automated chemical dosing to ensure an effective chemical program.
Perform sample conditioning. An essential part of an effective online measurement system is proper sample conditioning. This system should include total flow measurement, a back pressure device, and flow-indicating control valves for the analyzer branch lines. This setup will ensure you are establishing the desired flow and provide each measurement system with representative samples at an appropriate flow rate for consistent measurement.
Monitor several parameters. Monitor total chlorine, free chlorine, ORP, pH, and even conductivity for total dissolved solids tracking.
Ensure clean cooling water. The cleaner the water and the more accurate the instrumentation, the lower the risk of equipment damage, equipment underperformance, and contamination/corrosion in other systems.
Properly monitoring and controlling chlorine dosing for cooling water systems helps control microorganisms responsible for cooling system fouling, downtime, heat exchange efficiency, and even corrosion damage. Precise monitoring and control reduce chemical, maintenance, and production downtime costs.
With nearly 100 years of experience, Sentry Equipment can provide an integrated cooling water sample system that helps power plants maximize performance. Our proven solutions are vendor inclusive and can be supplied in a rack format or environmentally suitable enclosure. Contact us through our online contact form.
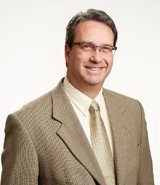
Written by John Powalisz
John Powalisz, Director of International Sales, is dedicated to sharing his technical expertise and knowledge of sampling equipment and systems in power plants, refineries, chemical and food processing facilities garnered from more than 19 years with the company. John has worked with clients worldwide to help them to comply with regulations and optimize processes by applying proper sampling hardware and techniques. While he is well-versed in all Sentry products and applications, he is particularly focused on the food and beverage and power generation markets as well as emerging market development.
Related Posts
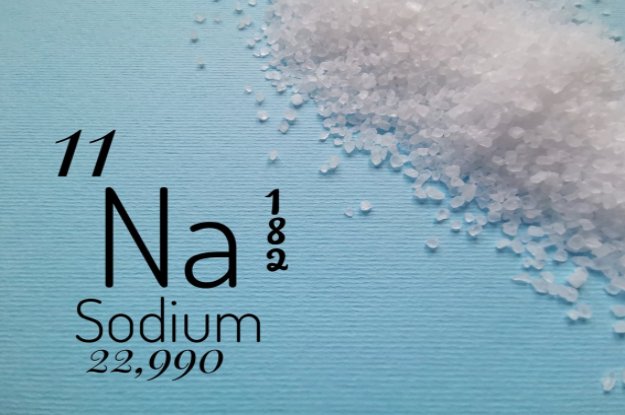
Preventative Maintenance
Monitoring Sodium in Power Plants
An increase in sodium measurements may identify unwanted dissolved impurities. When coated on the boiler turbine blades and heat exchanger surfaces, these impurities can cause catastrophic problems in power plants.
Read More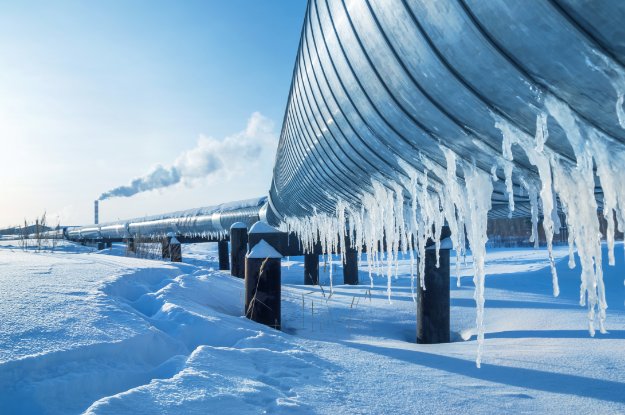
Preventative Maintenance
Avoid a Pipeline Freeze with a Methanol Injection Plan
As temperatures drop, equipments risk of damage increases.
Read More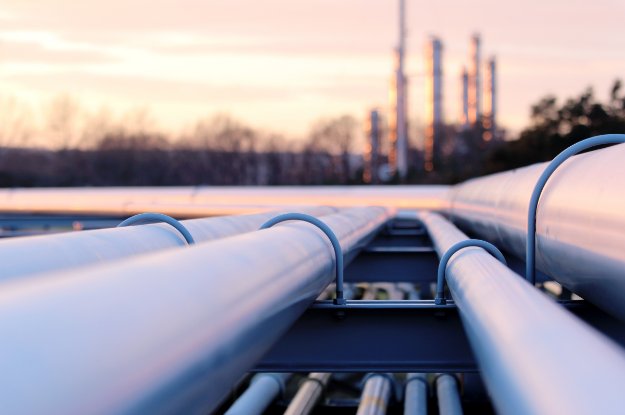
Preventative Maintenance
CASE STUDY: Prevent Equipment Downtime due to Crude Oil Leaks
A G50 Crude Oil pipe may cause significant damage to machining operations, equipment, and employee safety within a facility.
Read More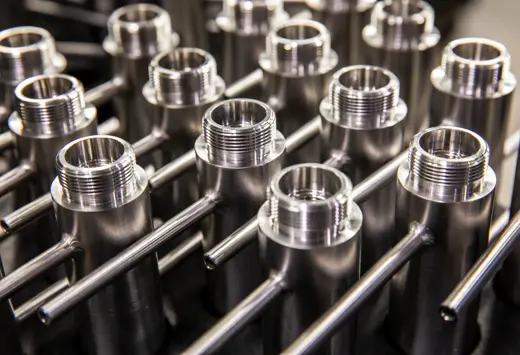
Protect Your SWAS
Sentry's sampling accessories ensure that you can maintain precise temperatures and/or pressures.