Understanding the Challenges in HRSG Water and Steam Monitoring
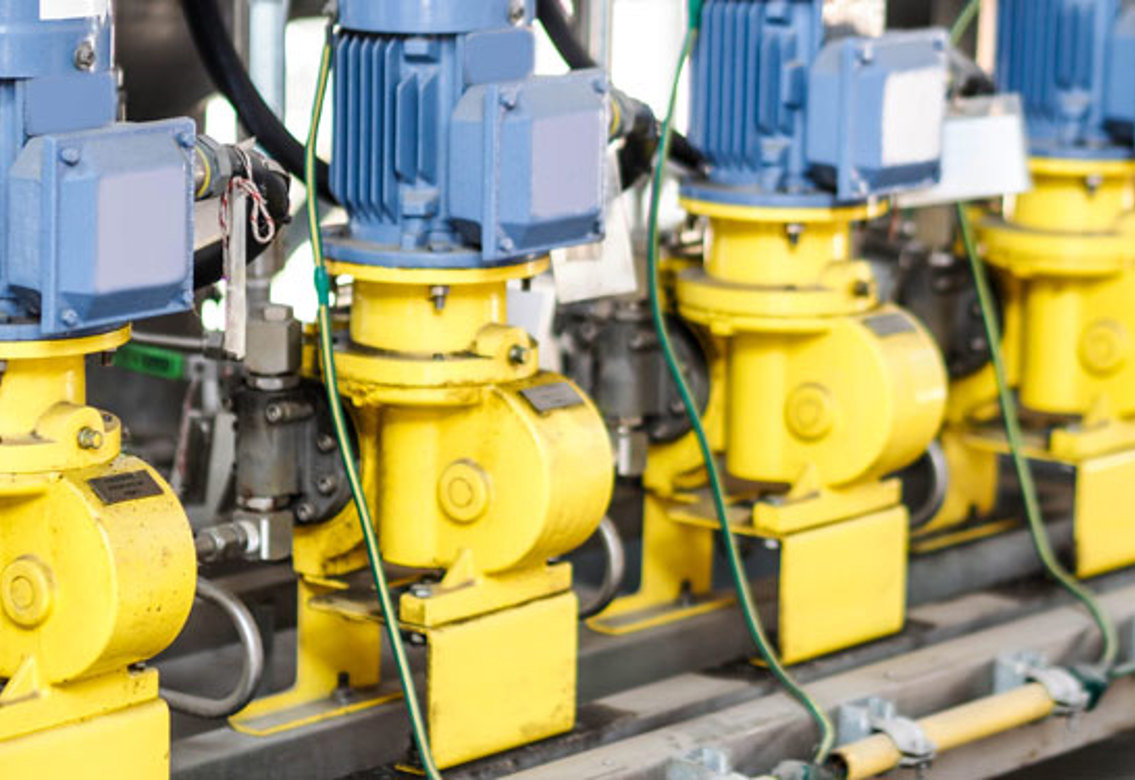
Heat Recovery Steam Generators (HRSGs)
However, as many HRSGs operate at high temperatures and pressures, harsh conditions can transform seemingly minor chemistry upsets into major problems.
When working with these units, outages and employee safety are two primary concerns of poor water/steam chemistry.
Online water/steam chemistry monitoring is critical not only for normal chemistry control but also to detect upsets. However, if samples are not extracted and conditioned properly, the data may give false indications of actual conditions in the unit.
A new article in Hydrocarbon Processing examines three primary issues regarding HRSG water/steam monitoring. In it, you’ll learn about:
- Selecting the critical measurements to monitor normal operating conditions, establish chemical feed control to maintain normality, and detect chemistry upsets.
- The extreme importance of proper sample extraction and conditioning to ensure that online instrument data is accurate.
- The benefits of iron monitoring are particularly important for tracking flow-accelerated corrosion (FAC), which can serious accidents. These measurements provide direct data on the efficacy of steam generator chemical treatment programs.
Combined cycle power generation has evolved into a bridge technology as the US, and much of the world, transition away from coal-fired units to renewables and other low-carbon technologies. HRSGs are an important part of combined cycle plants, where diligent monitoring and control of water/steam chemistry is essential for reliable operation.
Read more at “HRSG Water/Steam Sampling: Do It Right or Face Potential Consequences” in Hydrocarbon Processing by John Powalisz, Director of Business Development at Sentry Equipment, and Brad Buecker from ChemTreat.
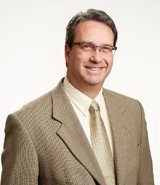
Written by John Powalisz
John Powalisz, Director of International Sales, is dedicated to sharing his technical expertise and knowledge of sampling equipment and systems in power plants, refineries, chemical and food processing facilities garnered from more than 19 years with the company. John has worked with clients worldwide to help them to comply with regulations and optimize processes by applying proper sampling hardware and techniques. While he is well-versed in all Sentry products and applications, he is particularly focused on the food and beverage and power generation markets as well as emerging market development.
Related Posts
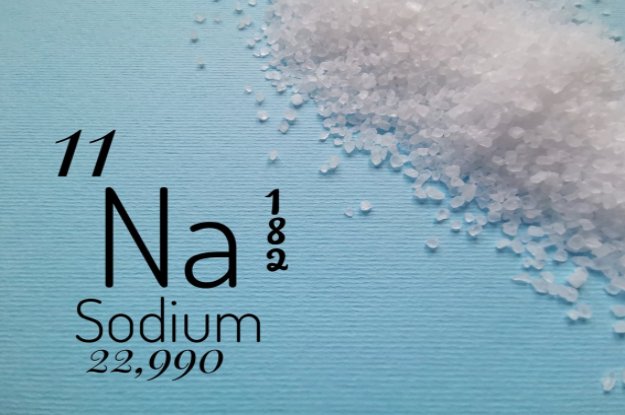
Preventative Maintenance
Monitoring Sodium in Power Plants
An increase in sodium measurements may identify unwanted dissolved impurities. When coated on the boiler turbine blades and heat exchanger surfaces, these impurities can cause catastrophic problems in power plants.
Read More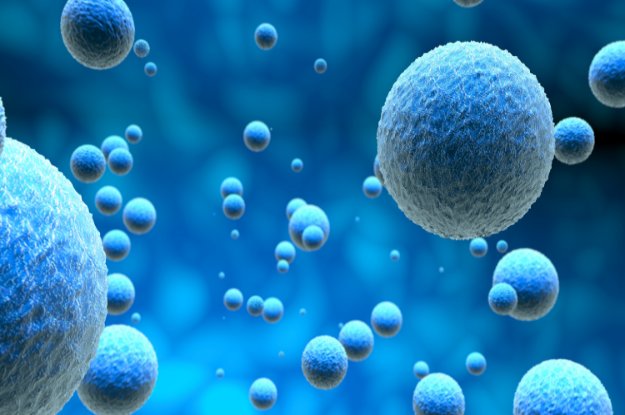
Preventative Maintenance
The Advantages of Chlorine Dosing to Control Biofilm in Industrial Cooling Systems
Microorganisms are organisms of microscopic size, which may exist in its single-celled form or as a colony of cells such as bacteria, fungi, and algae.
Read More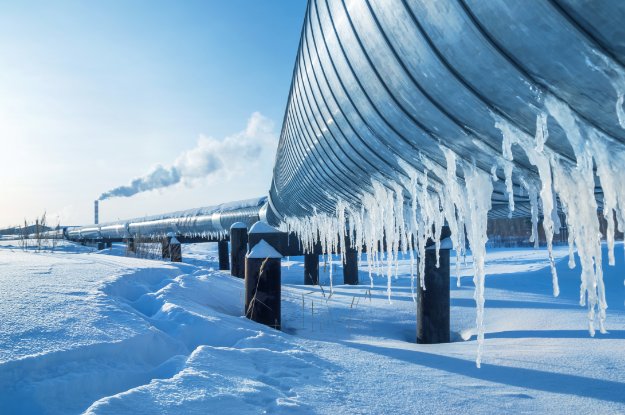
Preventative Maintenance
Avoid a Pipeline Freeze with a Methanol Injection Plan
As temperatures drop, equipments risk of damage increases.
Read More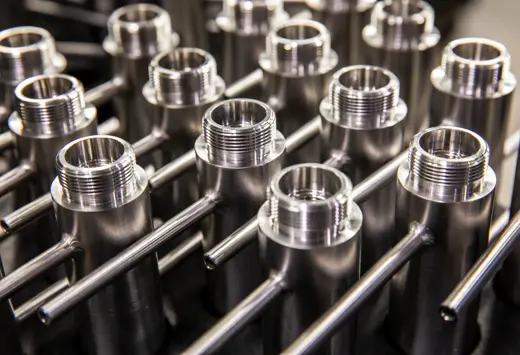
Protect Your SWAS
Sentry's sampling accessories ensure that you can maintain precise temperatures and/or pressures.